FEEL FREE TO ASK US
FREQUENTLY ASKED QUESTIONS
To provide clarity on our services, we have compiled answers to frequently asked questions regarding die moulds, die casting, prototyping, and manufacturing.
- Quality
- Accuracy
- Safety
- Reliance
GENERAL QUESTIONS
Frequently asked questions
DSW provides immediate pricing and lead times for your custom parts. There are one methods to obtain a quotation and Design for Manufacturability (DFM) feedback from our sales team:
Send one or more 3D CAD files directly to [email protected] or [email protected].
In most cases, we respond with a quotation within 24 business hours of receiving a Request for Quotation (RFQ). Should there be any delays, we will inform you at the earliest opportunity.
For quoting, DSW prefers 3D CAD files in formats like STEP, IGES, X_T, or STL. 2D CAD drawings with reference dimensions should be in DWG or PDF format. All DSW processes rely on accurate 3D CAD solid models
Yes, die casting is a high-volume process that requires specialised tools and moulds. The minimum quantity depends on the option you choose:
- Economy: 500 pieces
- Domestic: 1000 pieces
For smaller quantities, we suggest considering our CNC machining process.
Die casting is a metal casting process characterized by forcing molten metal under high pressure into a mold cavity. The mold cavity is created using two hardened tool steel dies which have been machined into shape and work similarly to an injection mold during the process. Most die castings are made from non-ferrous metals, specifically zinc, copper, aluminum, magnesium, lead, pewter, and tin-based alloys.
Commonly used materials in die casting include:
-
- Aluminum Alloys: Lightweight, high strength, and good corrosion resistance.
- A380 / 380.0
- A360 / 360.0
- A413 / 413.0
- ADC12
- B390.0
- C443.0
- 383.0
- 384.0
- 518.0
-
- Zinc Alloys: Low melting point, high ductility, and good impact strength.
- Zamak-2
- Zamak-3
- Zamak-5
- Zamak-7
- ZA-8
- ZA-12
- ZA-27
-
- Magnesium Alloys: Lightweight and good mechanical properties.
- AZ91D
- AM60B
- AS41B
Die casting is widely used in various industries, including:
- Automotive: Engine blocks, transmission housings, and other critical components.
- Electronics: Housings for devices, heat sinks, and connectors.
- Industrial Equipment: Pumps, valves, and other machinery components.
- Consumer Products: Appliances, hand tools, and hardware.
The main die casting processes are:
- Hot-Chamber Die Casting: Suitable for metals with low melting points like zinc, magnesium, and lead alloys.
- Cold-Chamber Die Casting: Used for metals with high melting points such as aluminum, brass, and copper.
TECHNICAL QUESTIONS
Frequently asked questions
We provide a range of manufacturing services, including Aluminum Die Casting, CNC Machining, Injection Molding, 3D Printing, Sheet Metal Fabrication, Metal Stamping, and Surface Finishing Services.
We operate ten die casting machines, each with a dedicated melting furnace, ranging from 300 to 1,600 tons. This setup allows us to produce components of various sizes, accommodating diverse production needs.
Yes, we offer OQC reports upon request. Once the order is completed, we can provide a dimensional inspection report for 6 pieces, along with original material certifications, inspection reports, and certificates of conformance.
Yes, at DSW we provide post-machining for die cast parts, ideal for achieving critical tolerances or meeting specific surface roughness requirements that die casting alone cannot fulfil. These options can be selected during the quoting process.
After placing an order, tooling must be fabricated, with part samples delivered in 12-18 weeks. Additional time is required to complete production after sample approval. Lead times can vary based on project specifics, and our expert team will work closely with you to ensure the best turnaround time.
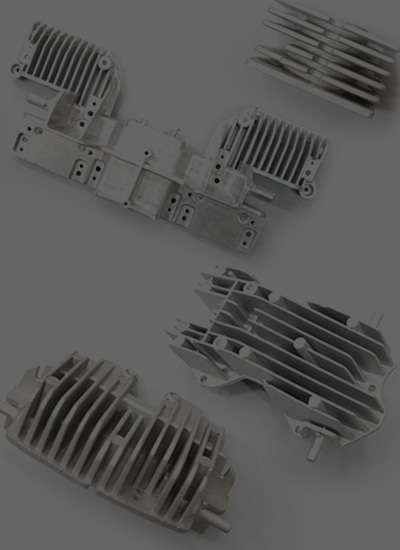
Ask Us
Quick contact form