Understanding QC, IQC, IPQC, and QA in Manufacturing Quality Management
Maintaining high-quality products is paramount in the manufacturing industry. This requires a well-structured quality management system incorporating various quality control and assurance facets. This article examines the differences and roles between quality control, incoming quality control, in-process quality control, and quality assurance.
Quality Control (QC)
Quality Control in die casting encompasses all activities to ensure that products meet specific quality standards. QC primarily focuses on monitoring the production stages, identifying defects in finished products, and preventing the delivery of non-conforming goods to customers. QC activities include:
- Design Quality Control (DQC): Inspection of product designs to ensure they meet predefined standards.
- Incoming Quality Control (IQC) involves Inspecting raw materials and components upon arrival to ensure they comply with quality specifications.
- In-Process Quality Control (IPQC): Ongoing inspections during the manufacturing process to identify and correct defects.
- Final Quality Control (FQC): Inspection of finished products before they are shipped to customers.
- Outgoing Quality Control (OQC) is the final check before products leave the factory to ensure they meet customer requirements.
Incoming Quality Control (IQC)
IQC involves inspecting all incoming materials, such as raw materials, components, and packaging. Key responsibilities include:
- Conducting inspections according to predefined standards.
- Maintaining detailed inspection records.
- Report any abnormalities and coordinate with suppliers to resolve issues.
- Ensuring that only quality materials enter the production process.
In-Process Quality Control (IPQC)
IPQC focuses on monitoring the production process to ensure that quality standards are maintained throughout. Key activities include:
- Regular inspections and audits at various stages of production.
- Recording inspection results and suggesting corrective actions for identified issues.
- They ensure that any detected defects are addressed immediately to prevent defective products from advancing to the next stage.
Quality Assurance (QA)
QA involves systematically managing all activities and processes that contribute to product quality. Unlike QC, which is reactive, QA is proactive, aiming to prevent defects through a robust quality management system. QA tasks include:
- Establishing and maintaining quality standards and procedures.
- Conducting internal audits to ensure compliance with quality standards.
- Coordinating with various departments to improve quality.
- Providing training and guidance to staff on quality-related issues.
- Reviewing, revising and approving documentation related to quality standards and processes.
Differences Between QC and QA
While both QC and QA aim to ensure product quality, they operate differently. QC focuses on identifying and correcting defects in finished products, while QA focuses on preventing defects by ensuring that processes and systems are appropriately managed. In essence:
- QC: Inspects products and eliminates defects.
- QA: Establishes systems to avoid defects and ensures compliance with quality standards.
Roles of QA and QC:
Work Perspective
- QA (Quality Assurance): Focuses on preventing product issues by ensuring correct production procedures and achieving quality control goals.
- QC (Quality Control): Identifies potential problems in semi-finished/finished products, confirms if products meet customer requirements and specifications, and monitors product quality.
Technical Perspective
- QC: Conducts inspections against specifications, finds potential issues, and audits control methods.
- QA: Identifies problem areas and root causes, provides solutions to prevent recurrence, and records improvements systematically through 8D Reports or QC Stories, requiring high professional knowledge and technical expertise.
Goal Perspective
- QA: Aims to meet customer requirements, gain trust, and institutionalize management throughout the product lifecycle by establishing a quality management system, creating documentation, and verifying compliance with customer requirements.
- QC: Implements techniques and methods to ensure products meet quality standards, including inspection, correction, and feedback, primarily within the factory.
Responsibilities of IPQC, IQC, and QA in Manufacturing
IPQC Responsibilities
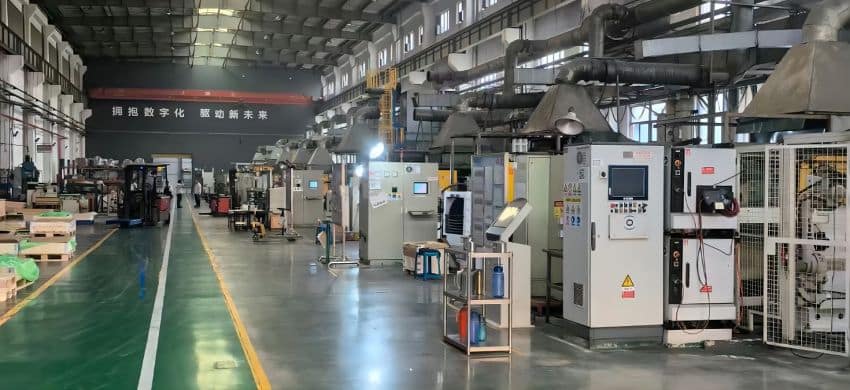
- Inspect products during production and maintain records.
- Complete inspection reports based on recorded data.
- Propose improvements for any issues found during the inspection.
IQC Responsibilities
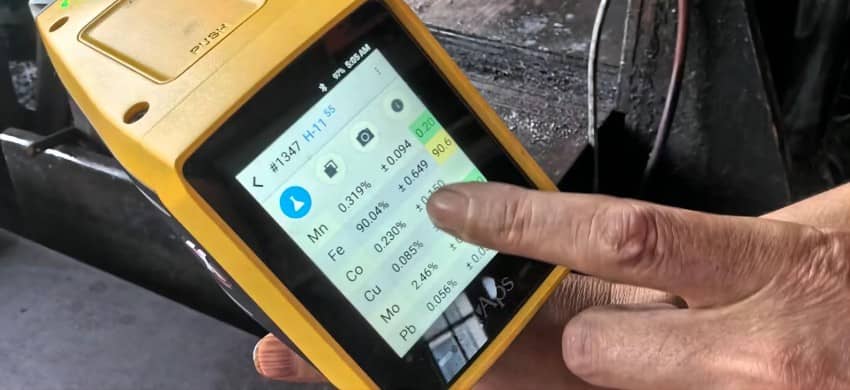
- Inspect raw materials per standards.
- Accurately fill out inspection records.
- Maintain testing equipment.
- Report any abnormalities in raw materials.
- Identify and manage raw materials.
- Sign and receive inspection reports from warehouse staff.
- Re-inspect stock materials for quality issues raised by the production line.
QA Responsibilities
- Oversee departmental operations, ensuring GMP compliance.
- Supervise and correct quality-related issues across the enterprise.
- Review and approve inspection results and production configurations.
- Evaluate pilot test plans and new product developments.
- Handle and improve quality complaints from users.
- Conduct comprehensive GMP inspections annually in collaboration with relevant departments and report findings to company leadership.
How They Work Together
Different quality control processes work together in a well-structured manufacturing quality management system to ensure consistent and high-quality output from start to finish. Each stage serves a distinct role:
- IQC ensures that the materials and components entering production are of the required quality.
- IPQC monitors and controls the production process, ensuring consistent quality at every stage.
- QC inspects the final product to confirm it meets the desired specifications.
- QA oversees the entire process, focusing on preventing defects through process improvement and system design.
Together, these quality control mechanisms form a robust framework for manufacturing. This integrated approach ensures that every step of the production process, from the selection of materials to the final product, is rigorously managed. Manufacturers can reduce production costs, minimize waste, and improve customer satisfaction by maintaining high standards.
TQC and Modern Quality Systems
TQC serves as a foundation for several modern quality systems, including:
- Total Quality Management (TQM): TQM, or total quality management, is a development of TQC that emphasizes customer satisfaction and constant improvement. TQC goes beyond these discrete activities to include everyone in the company—from senior management to manufacturing workers—in the search for excellence. Unlike conventional quality control techniques, which concentrate primarily on final product inspections, TQC stresses quality at every manufacturing level. It aims for long-term success using internal process improvement and employee involvement, including quality in all corporate activities.
- Six Sigma: Six Sigma is a data-driven approach to reducing flaws through statistical analysis. It emphasizes lowering variability, enhancing process efficiency, and reaching almost ideal quality standards.
- Lean Manufacturing: Although its primary goal is waste elimination, streamlining manufacturing techniques improves quality. Lean helps lower mistakes and flaws by stressing efficiency and eliminating pointless procedures.
Conclusion
Quality Control (QC) and Quality Assurance (QA) play an integral part in manufacturing quality products. QC ensures defective items are identified and remedied before reaching customers, while QA checks on production processes to ensure product creation remains robust and effective. By effectively understanding and applying both methods, manufacturers can enhance product quality while meeting customer expectations and remaining competitive.
References:
1. Allion Labs. “Things You Must Know about QA and QC.” Retrieved from Allion Labs.
2. Dozuki. “A Deeper Look Into Quality Assurance vs. Quality Control in Manufacturing.” Retrieved from Dozuki.
No comment