Metal Injection Moulding (MIM) is a specialized manufacturing process similar to plastic injection molding but involves additional steps to create small, complex metal parts. This technique is integral to producing components weighing between 1 and 100 grams, particularly where precision and high-volume production are required. This article provides an in-depth look at the MIM process, its applications, advantages, and disadvantages.
What Is Metal Injection Moulding?
Metal Injection Molding (MIM) begins with a polymerized metal feedstock composed of fine metal particles mixed with a plastic binder. This feedstock is injected into a mold cavity under high pressure, similar to plastic injection molding. However, MIM parts undergo several additional steps:
- Injection Molding: The feedstock is injected into the mold to form “green parts.”
- De-binding: The plastic binder is removed, resulting in porous “brown parts.”
- Sintering: The brown parts are heated to high temperatures in a furnace, fusing the metal particles into dense, non-porous metal parts. Shrinkage is accounted for during mold design.
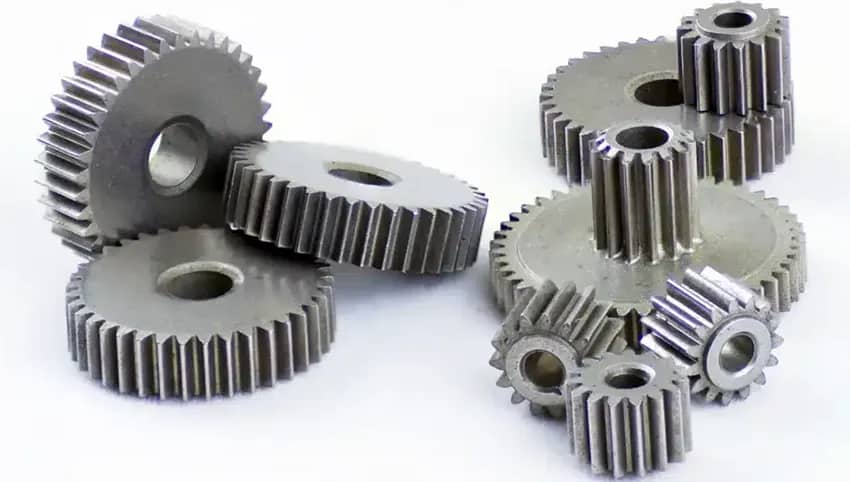
Purpose and Applications of Metal Injection Molding
MIM is ideal for producing small, intricate metal parts in high volumes, providing an efficient alternative to traditional manufacturing processes like machining, casting, and forging. MIM is widely used in various industries, including:
- Automotive: Manufacturing sensor housings, gear synchronizers, fuel injectors, and fasteners.
- Aerospace: Production of complex components that meet stringent weight and strength requirements.
- Medical: Fabrication of surgical instruments, implants, orthodontic brackets, and dental crowns using biocompatible metals.
- Electronics and Telecommunications: Micro-electromechanical systems (MEMS), connectors, and shielding components are created.
- Consumer Goods: Production of precision parts such as watch cases, eyeglass frames, and mechanical components in high-end consumer products.
Comparison with Plastic Injection Molding
Both MIM and plastic injection molding involve injecting material into a mold cavity. However, the key differences include:
- Materials: MIM uses metal powders, while plastic injection molding uses polymers.
- Post-Processing: MIM parts require de-binding and sintering, unlike plastic parts, which are typically completed upon ejection.
- Applications: MIM is suited for small, intricate parts, whereas plastic injection molding can produce a broader range of part sizes and complexities.
Materials Used in MIM
The versatility of MIM is evident in the wide range of materials it can utilize. These materials are categorized as follows:
- Ferrous Alloys: Steel, stainless steel (316, 316L, 17-4 PH, etc.), tool steel, iron-nickel alloys, invar, Kovar.
- Tungsten Alloys: Tungsten and its alloys are challenging to machine.
- Hard Metals: Cobalt-chromium, cemented carbides, cermets, known for their wear resistance and hardness.
- Special Metals: Aluminum, titanium, nickel, and molybdenum, offering unique properties for specific applications.
Usability of Specific Metals
- Tin: Not suitable for MIM in pure form but can be used as an alloying element.
- Tungsten: Favorable for MIM due to the difficulty of machining tungsten through traditional methods.
MIM Metals and Powders Available Through DSW
Alloy Group | Specific Alloys | Description |
Stainless Steel | 316, 316L, 17-4 PH, 303, 304, 440C, 420P | Steel alloys with high nickel and chromium increase corrosion and heat resistance.
Ideal for surgical tools in the medical industry. |
Low-Alloy Steel | Fe-Ni (Iron-Nickel), FN02, FN08, 4140, 8620, 100Cr6 | Low carbon content and low alloying elements improve machinability and cost-effectiveness. |
Tool Steel | M2 | High carbon content provides high hardness and abrasion resistance, making it perfect for cutting tools and mold. |
Soft Magnetic Steel | Fe-Ni50, Fe3Si, FeCo50, FeCoV | High magnetic permeability makes these steels ideal for solenoids, electric motors, and relays. |
Tungsten Heavy Alloy | W-Ni-Fe (Tungsten Nickel Iron), W-Ni-Cu (Tungsten Nickel Copper) | Composed of tungsten with other alloying elements, used mostly for electromagnetic shielding due to high density. |
Tungsten Carbide-Cobalt (WC-Co) | Tungsten Carbide-Cobalt | Cobalt particles increase hardness and wear resistance and are suitable for cutting tools, machine parts, and mining tools. |
Process Duration and Quality
The MIM process takes between 24 and 36 hours from powder to finished parts. Most of this time is spent on thermal de-binding, which can take up to 24 hours. MIM parts typically achieve 96%- 99% density post-sintering, producing high-quality components with minimal porosity and high precision.
Advantages of Metal Injection Moulding
- High Volume Production: Efficiently produces large quantities of complex parts.
- Design Flexibility: Fewer design restrictions compared to other metal processes.
- High-Quality Surface Finish: Excellent surface quality with options for further post-processing.
- Material Efficiency: Up to 95%-98% material utilization, reducing waste.
- Mechanical Properties: Superior hardness and strength.
- Cost-Effective for High Quantities: More economical than machining and sometimes stamping for large production runs.
Disadvantages of Metal Injection Molding
- High Initial Investment: Significant costs for tooling and setup.
- Limited to Small/Medium Parts: Larger parts increase production costs.
- Shrinkage Considerations: Parts shrink during sintering, which must be offset in the mold design.
Recent Advancements and Future Trends
Recent advancements in MIM technology include:
- Enhanced Feedstock: Development of more refined metal powders and binders to improve part quality and reduce porosity.
- Process Automation: Automation integration in the MIM process to enhance efficiency and consistency.
- Hybrid Techniques: Combining MIM with other manufacturing processes, such as additive manufacturing, to create complex components.
Future trends indicate a growing adoption of MIM in emerging industries, such as:
- Biotechnology: Custom implants and prosthetics.
- Renewable Energy: Components for wind turbines and solar panel systems.
- Advanced Electronics: Miniaturized components for IoT devices and wearable technology.
Accuracy and Popularity
MIM offers high accuracy with dimensional tolerances of +/- 0.3% -0.5 %. Its popularity has surged, and the global market, driven by its productivity and cost-efficiency, is expected to grow from $4,120 million in 2022 to $8,020 million by 2030.
Comparison with Die Casting
Die casting is often more cost-effective for significant parts and requires less post-processing. However, MIM excels in producing smaller, intricate parts with high precision. While the initial injection stage of MIM is faster, the overall process, including post-processing, makes die casting quicker for specific applications.
Metal Injection Molding (MIM) is a highly efficient and precise manufacturing process, ideal for high-volume production of small, intricate metal parts. It offers numerous advantages, including design flexibility, high-quality output, and material efficiency, making it a valuable choice across various industries. For those seeking a reliable MIM manufacturer, DSW provides comprehensive MIM services to meet your production needs.
No comment