Exploring the Diverse Types of CNC Machines and Their Applications
CNC (Computer Numerical Control) machines have revolutionised modern manufacturing, offering unparalleled precision, efficiency, and versatility across a wide range of industries. From aerospace to medical manufacturing, CNC machines enable the production of complex components with minimal human intervention, enhancing both productivity and quality.
In this article, we explore the various types of CNC machines, their functions, and their applications, providing a comprehensive guide to understanding this critical technology.
What Is CNC Machining?
CNC machines operate using pre-programmed instructions created through CAD (Computer-Aided Design) software. Once the design is finalised, it is translated into G-code, a machine-readable language that instructs the CNC machine on how to perform precise operations, such as cutting, drilling, or shaping materials.
CNC machines are highly adaptable, available in various forms, and capable of executing a multitude of tasks, making them indispensable in modern manufacturing.
An Overview of CNC Machine Types
Below, we delve into the most common types of CNC machines, each uniquely suited to specific tasks and materials:
Types of CNC Machines
CNC milling machines
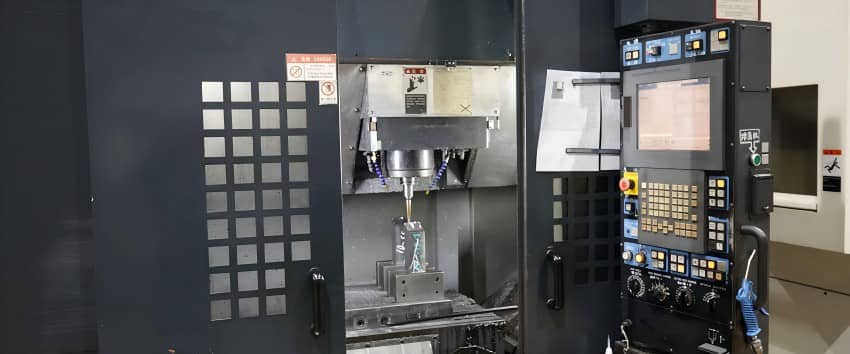
CNC milling machines are among the most widely used types, ideal for shaping hard materials through drilling, cutting, or shaving operations. These machines utilise rotary cutting tools that move along multiple axes (typically 3 to 6) to create complex shapes. Milling machines are commonly employed in industries like automotive and aerospace to produce high-precision components.
CNC Lathes
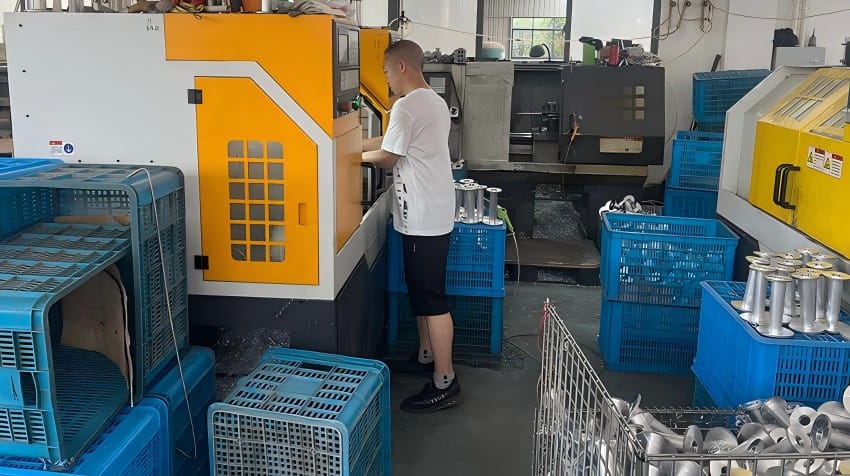
CNC lathes differ from milling machines in that the workpiece rotates while the cutting tool remains stationary. This method is particularly effective for producing cylindrical, conical, or spherical shapes. CNC lathes are widely used in metalworking, particularly for creating parts such as shafts, pulleys, and other round components.
The rotation of the workpiece allows for the precise removal of material, shaping it into the desired form. This method is highly effective for creating symmetrical objects along a central axis.
CNC Routers
CNC routers are often used for large-scale 2D and 3D projects, including cutting wood, aluminium, steel, and plastic sheets. Operating along the Cartesian coordinate system (X, Y, Z axes), these machines excel at producing intricate designs and patterns, making them popular in furniture manufacturing, signage, and cabinetry.
Pick and Place Machines
Pick and place machines are essential in the electronics industry, particularly for assembling circuit boards. These machines use vacuum nozzles to pick up tiny components and accurately position them on boards, significantly speeding up the assembly process for devices such as smartphones, laptops, and tablets.
Laser and Plasma Cutters
Laser and plasma cutters serve similar purposes but differ in their cutting methods. Laser cutters use concentrated light beams to achieve intricate, detailed cuts, ideal for thin materials. In contrast, plasma cutters use ionised gas to cut through thicker metals. Both are commonly used in metal fabrication, automotive bodywork, and artistic design.
Custom-Built CNC Machines
Custom-built CNC machines are designed to meet specific requirements, often incorporating the latest technological advancements to handle unique tasks. These machines are tailored to particular industries and can include features like additional axes, specialised tooling, and enhanced automation capabilities.
3D Printers
While 3D printers are technically CNC machines, they are unique because they use additive manufacturing rather than subtractive. Instead of removing material to shape an object, 3D printers build up layers of material to create the desired shape. 3D printing is rapidly growing in industries such as medical, aerospace, and prototyping, offering the ability to produce complex geometries that would be difficult or impossible with traditional methods.
The accuracy grade and tolerance grade of CNC machines are two key but distinct concepts that define machining precision. While both relate to the precision of mechanical processing, they each serve a specific purpose and are applied in different contexts.
Accuracy Grade of CNC Machines
The accuracy grade of a CNC machine refers to the level of precision it can achieve during the machining process. These grades reflect the machine’s capability under ideal conditions and are categorized as follows:
Grade 1 Accuracy: Provides machining precision up to 0.002 mm, typically used for high-precision parts such as precision components and molds.
Grade 2 Accuracy: Provides a precision of 0.005 mm, suitable for general mechanical machining and component manufacturing.
Grade 3 Accuracy: Provides a precision of 0.01 mm, often used for standard industrial products and routine workshop operations.
Grade 4 Accuracy: Offers precision of 0.02 mm, ideal for mass production where high precision is not required.
Another important factor is positioning accuracy, which measures how well the CNC machine can repeat precise movements over multiple cycles. This is typically quantified as positioning error.
Tolerance Grade
Tolerance grade refers to the allowable variation in the dimensions of mechanical parts. According to industry standards, tolerance grades are classified into 20 levels, ranging from IT01 (the highest precision) to IT18 (the lowest). The higher the grade number, the larger the permissible dimensional variation and the easier the machining process. Key levels include:
IT01: Represents the highest level of machining precision, used for extremely precise parts.
IT6: Ensures high uniformity and reliable mating of surfaces, commonly used for important mechanical fittings.
IT18: Represents the lowest precision level, suitable for parts that don’t require high accuracy.
Application and Distinction
Accuracy grade refers to the inherent capability of the CNC machine to maintain precision, while tolerance grade defines the permissible dimensional variation for manufactured parts. Understanding both is crucial for optimizing production processes, ensuring that components meet both functional and precision requirements effectively.
Applications and Industries
CNC machines are vital across numerous industries, including:
Aerospace: Precision components like turbine blades and engine parts.
Automotive: Engine components, gearboxes, and custom parts.
Medical: Custom implants, surgical tools, and prosthetics.
Electronics: Circuit boards, casings, and heat sinks.
General Engineering: Prototyping, custom fabrication, and specialised machinery.
Advantages of CNC Machines
CNC machines offer several benefits, including:
High Precision and Consistency: The automated nature of CNC machining eliminates human error, ensuring consistent results.
Increased Productivity: CNC machines can operate continuously, significantly boosting production rates.
Versatility: Capable of handling a wide range of materials, including metals, plastics, and composites.
Reduced Waste: Efficient material usage and precise cutting reduce waste and costs.
Challenges and Considerations
Despite their advantages, CNC machines do come with challenges. High initial costs, the need for skilled operators, and maintenance requirements can be significant barriers for smaller businesses. Additionally, understanding the specific needs of a project is crucial in selecting the right type of CNC machine.
Future Trends in CNC Machining
The future of CNC machining is increasingly intertwined with Industry 4.0 technologies. Advances in artificial intelligence, the Internet of Things (IoT), and robotics are driving the development of smarter, more autonomous CNC machines that can self-optimise, predict maintenance needs, and further reduce downtime. Moreover, there is a growing focus on sustainability, with innovations aimed at reducing energy consumption, recycling materials, and minimising the environmental impact of machining processes.
Conclusion
CNC machines have transformed manufacturing, offering precision, efficiency, and versatility that are unmatched by traditional methods. Whether producing intricate medical devices or large-scale aerospace components, CNC technology continues to push the boundaries of what is possible in modern engineering.
No comment