Understanding Casting Shrinkage: What It Is and What Affects It
Sand Casting, Investment Casting, and Gravity Casting
Metal casting shrinkage is a crucial phenomenon that impacts cast metal parts’ size, structure, and overall quality. It occurs when molten metal cools and solidifies, leading to a decrease in volume and dimensional changes. Shrinkage is responsible for many casting defects and can severely affect the final product’s mechanical properties. In this article, we will explore what casting shrinkage is, the defects it can cause, and the factors influencing it.
What is Casting Shrinkage?
Metal casting shrinkage refers to alloys’ reduced volume and size as they transition from a liquid state to a solid state during cooling. This Shrinkage takes place in three stages:
- Liquid Shrinkage occurs when molten metal cools and contracts before solidifying. The temperature drop causes the liquid to reduce in volume.
- Solidification Shrinkage: When metal reaches its freezing point and begins to solidify, its volume decreases as it transitions from a liquid to a solid phase.
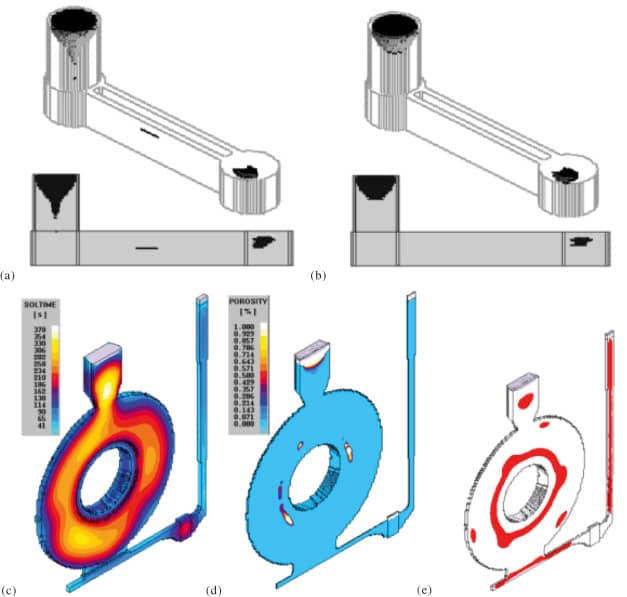
- Solid Shrinkage: After solidification, as the metal cools further to room temperature, it continues to contract. This type of shrinkage is usually referred to as linear shrinkage because it affects the size of specific dimensions, especially length.
The combined effects of liquid and solidification shrinkage are referred to as volume shrinkage, while solid Shrinkage, which occurs after the metal is solid, results in dimensional (linear) Shrinkage.
Casting Defects Caused by Shrinkage
Casting shrinkage can lead to various defects that affect the mechanical properties and functionality of the final product. These defects include:
- Shrinkage Cavity occurs when the liquid metal fails to fill the mold due to insufficient volume as it shrinks. This results in large, concentrated holes, typically seen at the last part of the casting to solidify.
- Shrinkage Porosity: Smaller, dispersed holes or voids can appear throughout the casting. These tiny cavities are typically found when insufficient molten metal fills the voids left by the solidifying metal.
- Internal Stress, Deformation, and Cracking: If solid Shrinkage is restricted or uneven, internal stresses build up, potentially leading to casting deformation or cracking. These stresses occur due to mechanical forces (such as mold restrictions) or thermal stresses (from uneven cooling).
These defects’ occurrence directly impacts the casting’s quality and strength. For instance, shrinkage cavities and porosity can compromise castings’ mechanical properties, while deformation and cracking can result in part failure during use.
Types of Shrinkage Defects
- Shrinkage Cavity: This defect appears when liquid and solidification shrinkage are not adequately compensated. It results in larger voids typically found at the last section of the casting to solidify.
- Shrinkage Porosity: A more dispersed form of Shrinkage, these small voids can significantly weaken the casting, especially in high-pressure applications. Shrinkage porosity can also lead to leaks in components tested for air or water tightness.
- Deformation and Cracking: Internal stresses arising from hindered solid Shrinkage can cause deformation or cracks in the casting. These stresses can be caused by uneven cooling or external forces from the mold.
The casting shrinkage described in the article applies broadly to all casting processes, as shrinkage is a fundamental phenomenon in metal casting. However, the specific context and defects mentioned suggest its relevance to several essential casting methods, depending on the situation:
1. Die Casting
- Shrinkage in Die Casting: Shrinkage in die casting is generally lower due to the high-pressure environment, which minimizes porosity. However, improper cooling or gating can still cause shrinkage-related defects.
- Applicability: The article can be adapted to highlight solidification shrinkage and porosity issues relevant to die-casting processes.
2. Investment Casting
- Shrinkage in Investment Casting: Investment casting often involves intricate and thin-walled parts. Shrinkage is a concern, especially in solidification, and must be addressed by careful mold and gating design.
- Applicability: Emphasis on reducing internal stresses and managing thermal gradients applies well here.
3. Sand Casting
- Shrinkage in Sand Casting: Shrinkage is more prominent in sand casting due to its lower cooling rates and the potential for inconsistent mold rigidity. Issues like shrinkage porosity and cavity formation are common.
- Applicability: Most of the defects and solutions in the article (e.g., risers for feeding) are highly relevant to sand casting.
4. Gravity Casting
- Shrinkage in Gravity Casting: Gravity casting relies on molten metal flowing into dies without external pressure. Shrinkage cavities are frequent, particularly in thicker sections, making riser design and solidification control critical.
- Applicability: Strategies for managing liquid and solidification shrinkage are directly relevant.
Reducing Shrinkage Defects
To minimize the risk of shrinkage defects, manufacturers use several methods:
- Risers and Runners: A riser acts as a reservoir for molten metal, allowing for the replenishment of metal as it solidifies, thereby reducing shrinkage cavities. Proper riser placement is crucial to transferring shrinkage-related voids to the riser rather than the final casting.
- Casting Design: Proper design adjustments—such as ensuring uniform wall thickness and avoiding localized metal build-up—can help reduce Shrinkage. A well-structured mold allows for more uniform cooling, which helps reduce internal stresses and prevent cracks.
- Optimizing Cooling: By adjusting cooling rates through chills and controlling mold materials, manufacturers can manage how quickly different casting parts cool and solidify. Even cooling helps prevent thermal stresses.
What Factors Affect Shrinkage?
Several factors influence the extent of Shrinkage in metal castings. These factors can be categorized into internal (material-related) and external (process-related) conditions.
- Alloy Type and Composition
The type of alloy used has a significant impact on shrinkage rates. Different materials have different thermal properties and solidification characteristics, affecting how much they shrink during cooling.
-
- Gray Cast Iron tends to have a smaller shrinkage rate than other alloys like cast steel. The solidification and cooling behaviour of the alloy play a significant role in how much Shrinkage occurs.
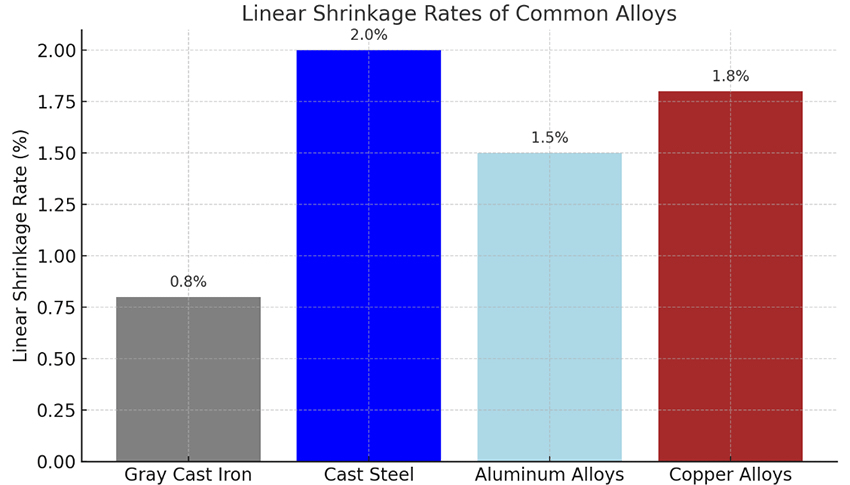
- Aluminum Alloys, for instance, tend to shrink more than iron alloys, requiring careful attention during the design and production processes.
- Process Conditions
Process conditions such as pouring temperature, mold design, and cooling rate significantly impact shrinkage.
- Pouring Temperature: The higher the pouring temperature, the greater the liquid Shrinkage. A hotter pour means more Shrinkage as the metal cools and solidifies.
- Casting Structure and Mold Material: Complex mold shapes and poor mold material yield can block the natural shrinkage process. The more complex the shape, the more difficult it is for the mold material to allow free Shrinkage.
- Mold and Core Design: The design of the mold and the cores used in casting can either facilitate or hinder Shrinkage. A mold with poor thermal conductivity or an unevenly designed structure may restrict Shrinkage, leading to stress and defects.
- Cooling Rate: Cooling is essential for solidifying and shrinking the casting. A uniform cooling rate across the casting minimizes thermal stress and the risk of cracking.
How to Control Shrinkage in Metal Casting
To control metal casting Shrinkage, the following techniques are commonly employed:
- Adjusting Pouring Temperature: A careful balance of pouring temperature ensures that metal cools consistently, minimizing Shrinkage.
- Optimizing Mold Design: Ensuring a simple, symmetrical design and consistent wall thickness across the casting helps reduce shrinkage stress.
- Using Risers and Chills: Risers provide additional molten metal to compensate for liquid Shrinkage, and chills can control the cooling rate to reduce thermal stress.
- Material Selection: Choosing alloys with lower shrinkage rates can help prevent shrinkage-related defects.
Conclusion
Casting shrinkage is an unavoidable part of the casting process, but it can be managed effectively with careful planning, design, and control of process parameters. Understanding the different types of Shrinkage and the factors influencing it allows manufacturers to produce higher-quality castings with fewer defects, improving the strength and reliability of the final product.
By following best practices in alloy selection, mold design, cooling methods, and process optimization, manufacturers can significantly reduce the impact of Shrinkage, resulting in better product outcomes and higher production efficiency.
Notes: The article best suits Sand Casting, Investment Casting, and Gravity Casting because these processes naturally allow Shrinkage within the mold environment and require detailed consideration of risers, cooling rates, and die design.
No comment