Achieving Dynamic Balance in Die Tool Making and Casting Processing
Achieving dynamic balance in die tool making is essential for producing high-quality, precise components. This involves focusing on key factors like gate balance, injection balance, and tooling design balance. Gate balance ensures the molten material flows evenly into the mold, while injection balance controls the pressure and speed during injection to prevent defects. Tooling design balance optimizes mold geometry to reduce stresses and ensure uniform part quality. By carefully addressing these elements, manufacturers can enhance part performance, reduce defects, and improve efficiency in high-precision industries like automotive and aerospace.
What is dynamic balance in die-casting bobbins?
Dynamic balance refers to the even distribution of mass around an object’s rotation axis. In the case of die-casting bobbins, which are often subjected to high-speed rotation, dynamic balance ensures that the mass is evenly distributed throughout the bobbin as it spins on the spindle of the textile machine. An imbalance in the bobbin can lead to several operational issues, including excessive vibration, premature wear, and potential damage to both the bobbin and the textile machine components.
Dynamic balance is critical to ensuring the bobbin runs smoothly and consistently at high speeds. It is a standard requirement in textile machinery, especially in high-speed winding and unwinding operations.
Steps for Achieving Dynamic Balance in Die Tool Making
1. Design Considerations:
Gate Balance: Ensure the gates are positioned to allow the uniform flow of molten material into the mold cavities. Uneven gate placement can cause imbalances and defects.
Injection Balance: Design the injection system to provide consistent pressure and flow rates to all parts of the mold. This includes selecting the appropriate injection points and ensuring the even distribution of material.
Tooling Design Balance: Consider the overall design of the tooling, including the weight distribution and symmetry. Ensure that the mold is balanced and does not favor one side.
2. Material Selection:
Choose materials with consistent density and mechanical properties. Variations in material properties can lead to imbalances during the casting process.
3. Precision Machining:
Use precision machining techniques to create die tools with tight tolerances. Any deviations in the tooling can cause imbalances in the final casting parts.
4. Simulation and Analysis:
Simulation software predicts the flow of molten material and identifies potential imbalances. This allows for adjustments before the actual die casting process.
5. Prototyping and Testing:
Create prototypes of the die tools and perform dynamic balance testing. Use the results to refine the design and ensure the final tools produce balanced parts.
6. Quality Control:
Implement stringent quality control measures throughout the die tool-making process. Regularly inspect and test the tools to ensure they meet the required standards.
Post-Casting Balancing Techniques
After die-casting, bobbins undergo post-production procedures to ensure dynamic balance. This often includes:
Balancing machines:
Specialized balance equipment measures the bobbin’s rotation and identifies imbalances. If we detect an imbalance, we remove or add material to the bobbin to achieve balance.
Vibration analysis:
Some manufacturers use vibration testing to assess how the bobbin behaves at high speeds. Adjusting the weight distribution can detect and correct any vibrations.
Tuning:
The shape or weight of the bobbin can be finely adjusted to meet the dynamic balance requirements for the textile machine.
Analysis of the Problem and Key Issues
Keyway Width:
A keyway is a groove or slot in die-casting bobbins typically used to accommodate a key. This small mechanical component helps secure the bobbin to whorls, preventing relative rotation. The keyway plays a critical role in the proper function of the bobbin, especially in high-speed applications such as textile machines.
Problem: The keyway ranges from 8.7 mm to 9.7 mm, while the required range is 9.14 mm to 9.397 mm. The keyway depth varies from 10.10 mm to 11.01 mm, whereas the specified range is 8.83 mm to 10.10 mm.
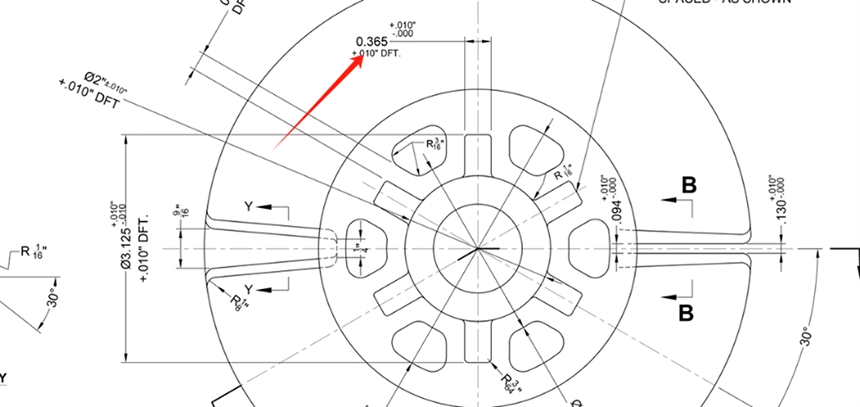
Explain: The standard casting tolerance is typically around ±0.3 to ±0.5 mm (IT8). This position does not require machining, but there is a draft angle.The keyway walls for die-casting bobbins also require drafting. Because the walls are slightly slanted, the width at the bottom of the keyway is slightly larger than at the top. The degree of the draft is typically specified based on the material, size of the part, and ease of mold release, but it can affect the accuracy of the final keyway width.
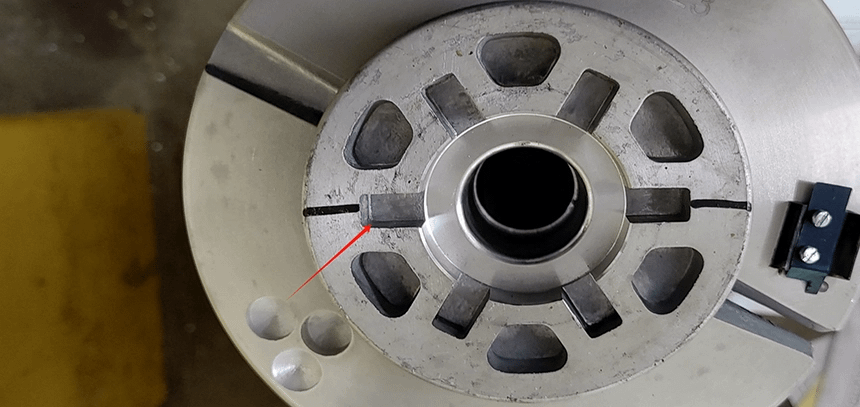
4. Sprue, Runner, and Gate: Guide Molten Metal Flow
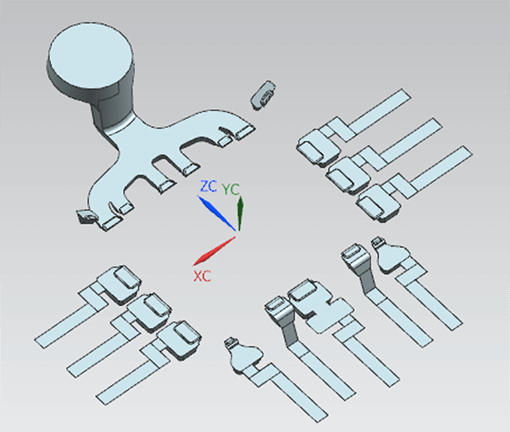
Ensuring effective injection of molten metal into the mold cavity without turbulence depends on the sprue, runner, and gate system, which also guarantees smooth flow and lowers flaws like cold shuts or voids.
The sprue is the point of entrance for molten metal entering the mold. Rising at the top of the mold, the sprue guarantees a regulated introduction of the metal. High-pressure die casting is usually used with a tapered form to hasten metal flow into the runner system. For significant parts like pump housings, the sprue design reduces air pockets and guarantees a constant metal flow.
Runner: This channel links the sprue to the gates, guiding the molten metal into the mold chamber. A well-made runner system guarantees a consistent fill by reducing the possibility of metal solidification before it enters the cavity. The runner system might have channels for complex castings, like those used in the car industry, so the molten metal can flow quickly into many cavities simultaneously, cutting down on cycle time.
The gate is the opening for molten metal used to reach the cavity. The gate’s size, form, and location determine how the metal fills the mold. A carefully placed gate ensures that the molten metal fills the mold evenly and without turbulence for a thin-walled item like a consumer electronics housing. Customizing gate design often requires matching the portion’s geometry to the metal’s flow characteristics.
5. Channels of cooling:
regulating the rate of solidification
Cooling is one of the most crucial elements of the die-casting process. It directly influences the solidification time and the quality of the final product. By absorbing heat from the molten metal integrated into the mold, cooling channels help control the cooling rate.
Channel design and mold material directly determine the efficiency of the cooling system. Developments in mold design, including conformal cooling channels that follow the form of the part, result in faster cooling rates and better casting quality. For example, conformal cooling systems are increasingly used in automobile die casting to produce parts with complicated geometries and strict tolerances since precise cooling channel design is crucial to prevent shrinkage, dimensional issues, or warping.
Ensuring airflow and avoiding defects in the vent system helps.
As molten metal is injected, proper ventilation is crucial for letting air and gases escape the mold. Inadequate venting can cause casting flaws such as air pockets, surface blebs, or insufficient fills.
Little channels or holes in the mold let gases and air escape during the injection. Proper ventilation ensures that the molten metal flows naturally into the hollow without getting caught by air. For medical devices with high-precision die casting, for instance, exact venting guarantees that gases do not cause porosity or weak areas in the finished item.
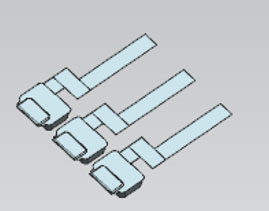
The vent system’s design must compromise economy and efficiency. Too much venting might cause the casting to lose molten or compromise its integrity. The best results are sometimes obtained by optimizing the vent placement using sophisticated simulation tools. Advanced venting systems are crucial in sectors like electronics, where components need great accuracy and limited tolerance for flaws to preserve product quality.
No comment