Cast vs Forged: Which Process Suits Your Needs?
Cast vs. Forged are essential metal-forming processes in various industries to create parts and components. Despite their shared purpose, these processes differ significantly in methodology and the characteristics of the resulting products. As a leading authority in metal forming and fabrication, we aim to clarify the distinctions between casting vs forging and help you determine which process best suits your project’s requirements.
What is Forging?
Forging involves shaping a solid piece of round metal bar using dies, pressure, and temperature. It can be classified in three ways:
- Temperature:Hot, warm, or cold forging.
- Type of Process:Open or closed die forging.
- Material Used:Steel forging, aluminum forging, brass forging, or bronze forging.
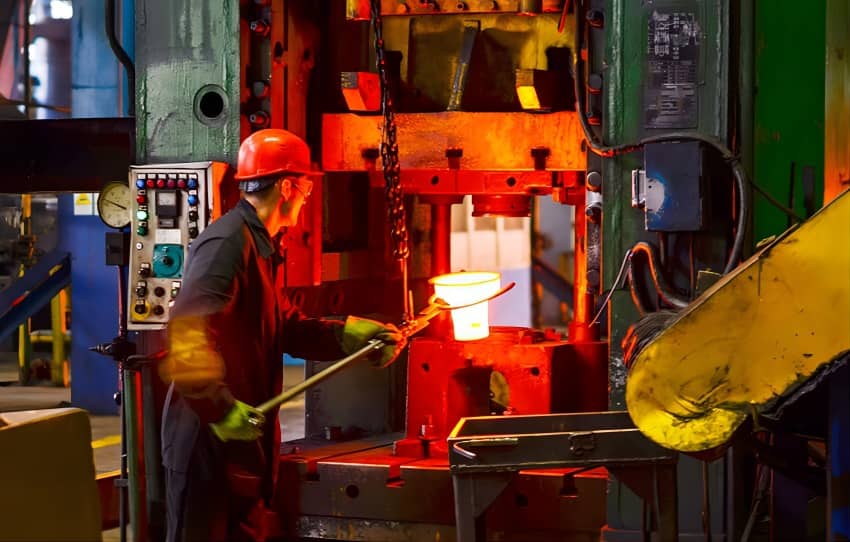
What is Casting?
Casting involves pouring molten metal into a hollow cavity mold, which cools to form a solidified part. The types of casting vary based on moulding materials, casting process, and filling pressures. The main metal casting methods include die casting, investment casting, permanent mold, and sand casting.
Forged vs. Cast: Key Differences
Casting and forging produce end products with distinct characteristics. Here’s a summary of their primary differences:
Factor | Metal Forging | Metal Casting |
Structural Integrity | Superior strength and material predictability | More porous and susceptible to breakage |
Tolerance | Not suited for highly complex geometries | Allows for high detail and tight tolerances |
Product Size | Limited by size and thickness; larger items are more difficult | Compatible with a wide range of sizes |
Material Selection | Limited selection of alloys | Compatible with nearly all types of metal |
Secondary Operations | Often requires additional refinement and finishing | Usually requires few secondary operations |
Cost | Cost-effective for medium to large production runs | Generally less expensive, but varies with the specific casting method |
Grain Flow: A Defining Factor
Grain flow is a crucial factor distinguishing these processes. In forging, the metal is deformed, but the grain flow remains unbroken, retaining its strength. Conversely, casting melts the metal, breaking the grain flow and reducing the initial strength once solidified. Thus, forged metal is less likely to shatter compared to cast metal.
Comparing Strength and Durability: Forged vs. Cast Bobbins
Forged components are 26% stronger than cast parts, meaning you get more durable bobbins without increasing weight.
They also have 37% greater fatigue strength, leading to a sixfold increase in their lifespan. This means a forged bobbin will last significantly longer.
Cast iron only has 66% of the yield strength of forged steel, which measures how much load a bobbin can handle before it starts to deform.
When tested to failure, forged parts show a 58% reduction in area, while cast parts only show a 6% reduction. This means forged bobbins can endure much more deformation before failing.
Which is Better: Casting or Metal Forging?
Choosing between casting and forging depends on your project’s priorities. Casting is often more versatile and cost-effective, making it great for complex shapes and exotic alloys. On the other hand, metal forging provides superior strength and structural integrity, making it ideal for applications that require high durability. Specifically, aluminum metal forging increases the strength of aluminum through strain hardening, maintains tighter tolerances, and reduces the risk of cracking or breaking.
Casting: Benefits, Defects, and Common Products and Industries
Casting is famous for producing complex and large-volume industrial parts. Benefits include:
- Complex Components: Allows for intricate internal and external features.
- Flexible Quantities: Suitable for high-volume production.
- Strength and Quality:Rapidly chills molten aluminum for strong, porosity-free components.
- Minimized Labor:Can be automated, reducing labor costs and errors.
- Low Cost:Reduced labor and material costs make casting economical.
Despite its benefits, casting can result in defects like interior tears or cracks. However, quality assurance technologies like X-ray machines help detect these defects before shipment.
Forging: Benefits, Defects, and Common Products and Industries
Forging, one of the oldest metal reshaping methods, offers several benefits:
- Stronger Products:Changes internal microstructure for denser components.
- Higher Fatigue Strength:Enhances mechanical properties, increasing stress resistance.
- Low Operating Cost:Requires fewer materials and less machining.
- Variety of Shapes:Suitable for industries needing high resistance and reliability, like automotive and aerospace.
Choosing between casting and forging involves weighing the specific requirements of your project. Casting is ideal for complex, low-cost components, while forging is best for applications demanding superior strength and structural integrity. Explore our past work to see how DSW’s metal forging and casting sourcing services can meet your project’s needs.
No comment