Cast Insert and Insert Casting
Augmenting the Utility of Cast Components
A cast insert, also known as a casting insert, is a component made from either metallic or non-metallic materials integrated into a casting during die-casting manufacturing. This process, known as insert casting, involves placing a prefabricated insert into the mold cavity before injecting molten metal. As the molten metal surrounds the insert and solidifies, it forms a permanent bond with the surrounding material. The result is a component combining the strengths of the base material and the inserted element.
In general, when designing die-cast parts, the designer must take into account the following seven aspects: wall thickness of the die-cast part, casting radii and draft angles, reinforcing ribs, minimum distance from casting holes to edges, rectangular holes and slots, inserts within the casting, and machining allowances. Before production, a professional designer should address these seven areas based on the actual requirements of the casting. It is important to emphasize that each aspect plays a significant role in the subsequent production of the die-cast part. Therefore, designers must pay special attention during the design process to ensure the design is reasonable and comprehensive.
Casting insert technology significantly enhances the mechanical properties of the finished product. Inserts are commonly used to improve strength, wear resistance, electrical conductivity, or threading capabilities—characteristics the base casting material may not provide. This technique is widely applied in the automotive, medical, aerospace, and electronics industries, where high-performance materials are essential. For example, insert casting improves component strength in automotive engines, resulting in more durable, high-performance parts.
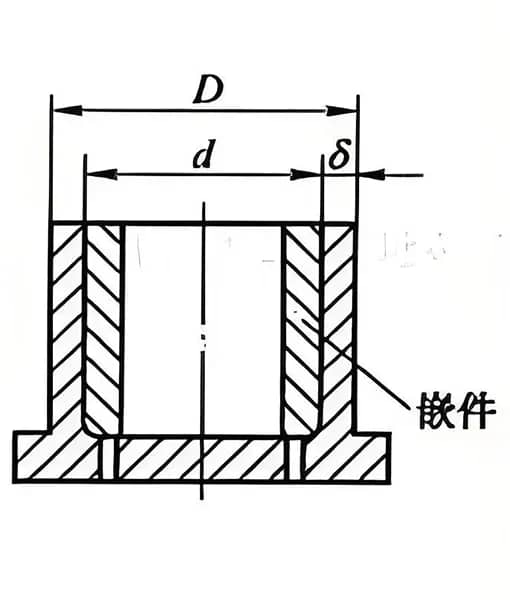
The Procedure of Insert Casting
The Department of Buildings promotes the safety build
The insert casting process commences with placing the casting insert into the mold chamber. Subsequently, molten metal—such as aluminum, zinc, or magnesium—is introduced into the mold. The molten metal circulates the insert and solidifies upon cooling, forming a strong link between the insert and the adjacent substance. This bond is crucial for maintaining the part’s mechanical integrity over diverse operating circumstances. Inserts can effectively improve and enhance the local processing performance of the die-cast part, such as strength, hardness, wear resistance, etc.
In vehicle manufacture, cast inserts are frequently employed to fortify components like engine mounts, augmenting their strength and capacity to endure extreme stress. This yields a component that is both more robust, more dependable, and enduring.
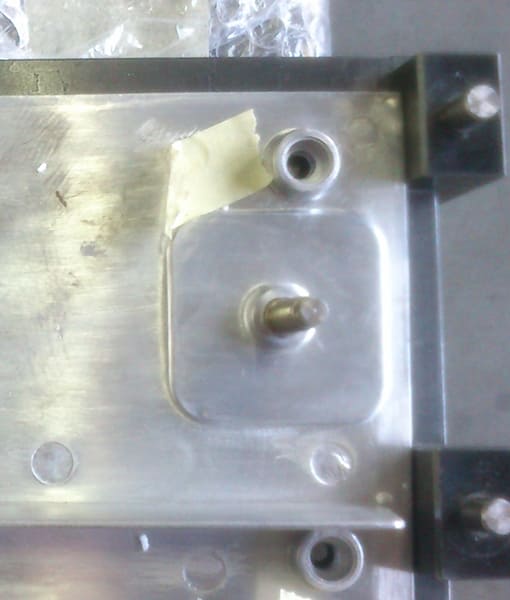
Castings Insert Design
Essential Factors When Employing Cast Inserts in Design
When developing components with casting inserts, meticulous attention must be paid to ensuring the insert is effectively integrated into the casting. Below are a few critical design considerations:
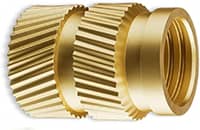
Secure Bonding: The cast insert must be securely affixed to the adjacent material to avert any displacement during the casting procedure. To secure the die-cast part, the insert must have grooves, protrusions, or knurling.
Avoid Acute Angles: Acute angles on the casting insert should be eschewed as they might complicate placement and generate stress concentration zones, potentially resulting in weak points in the component.
Positioning Stability: The insert’s position must be maintained throughout the casting procedure. Accurate mold design with precise tolerances guarantees proper alignment and prevents displacement.
Adequate Metallic Layer: The surrounding metal layer’s thickness must be sufficient to sustain the insert and preserve the structural integrity of the final component. If the next metal layer is fragile, the component may exhibit weakness or susceptibility to fracture.
Restrict Insert Quantity: To ensure cost-effectiveness and streamline the design, the quantity of inserts employed should be minimized judiciously. Excessive insert usage can unnecessarily elevate complexity and manufacturing expenses.
Electrochemical Corrosion Mitigation: When electrochemical corrosion between the insert and the casting poses a risk, the insert must be coated or treated to inhibit corrosion over time.
Refrain from Heat and Surface Treatment: Thermal treatments and surface coatings may compromise the adhesion between the insert and the casting. These treatments should be avoided unless explicitly required to maintain the integrity of the insert-casting bond.
Categories of Cast Inserts
Diverse types of casting inserts are employed throughout multiple industries, each tailored for specific functional requirements. These comprise:
Metal Inserts: Made of steel, brass, or stainless steel, metal inserts augment the strength of the casting or facilitate threading capabilities. Brass inlays are frequently used in electronic components because of their superior conductivity.
Threaded Inserts: These inserts establish a robust, resilient threaded region in the casting, which is especially advantageous when direct threading into the base material is unfeasible or would jeopardize the component’s integrity. Threaded inserts are frequently utilized in mechanical and automotive applications.
Applications of Insert Casting
Insert casting is extensively utilized in multiple industries, offering distinct benefits for varied applications. The adaptability of casting inserts renders them advantageous in numerous applications:
Threaded inserts are essential for components necessitating strong, resilient threads. Automotive components, such as engine parts, frequently necessitate threaded inserts to guarantee the secure attachment of bolts and screws.
Strength Augmentation: In sectors such as aerospace, components subjected to significant mechanical stress are enhanced by casting inserts that fortify the material. The insert enhances the overall strength of the component, rendering it more suitable for rigorous conditions.
Wear Resistance: More durable inserts can markedly enhance the wear resistance of a component. Industrial components in continuous contact with abrasive substances, such as gears or machinery parts, might be augmented with wear-resistant inserts to prolong their durability.
Electrical Components: Metal casting inserts are utilized to create electrical conduits within a component. This is crucial in the electronics sector, where establishing dependable electrical connections within the casting is important for functionality.
Request insert solutions!
Help you design and implement the perfect insert casting solution tailored to your specific needs.
Insert Casting vs. Overmolding
While insert casting embeds an insert into molten metal, overmolding typically involves molding plastic around an insert or another material, commonly used in injection molding rather than metal casting.
Advantages of Insert Casting:
- Reduces assembly time and costs by integrating components directly.
- Enhances the durability and mechanical properties of cast parts.
- Improves design flexibility by allowing multi-material combinations.
Insert casting is widely used in industries requiring precision-engineered, high-strength components with embedded features.
No comment