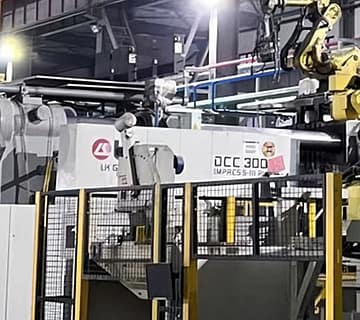
Top China Die Casting Manufacturers
Discover the top China die casting manufacturers in 2025, including industry trends, leading die casting factories, and innovations in automotive die casting factories. Learn about the latest China aluminium casting technology and how Chinese die cast companies are shaping the global market. ... Read More