Understanding Metal Gravity Casting
Metal gravity casting is one of the fundamental processes used to convert metal materials into desired products. This process, along with forging, extrusion, rolling, drawing, stamping, cutting, and powder metallurgy, is essential in manufacturing. Casting is the most basic, commonly used, and widespread method.
In gravity casting, molten metal is poured into a hollow mold made of high-temperature-resistant materials. As the metal cools and solidifies, it takes the shape of the mold, resulting in the final product, known as casting.
Types of Casting
-
- By Material:
-
- Ferrous Metal Casting: Includes cast iron and cast steel.
- Non-Ferrous Metal Casting: Encompasses aluminium alloy, copper alloy, zinc alloy, and magnesium alloy.
DSW specializes in casting various materials, including aluminium, copper, iron, magnesium, and zinc, which may not be suitable for high-pressure processes.
Aluminium gravity casting works effectively with various aluminium alloys, including under-list material. -
- By Material:
ASTM Standard | GB Standard | BS Standard | EN Standard |
A319 | ZL101 | LM6 | EN AC-42100 |
A356 | ZL101A | LM20 | EN AC-42200 |
A357 | ZL102 | LM25 | EN AC-43000 |
A413 | ZL107 | EN AC-43200 | |
EN AC-43300 | |||
EN AC-43400 | |||
EN AC-44200 | |||
EN AC-44300 | |||
EN AC-46000 | |||
EN AC-46200 |
- By Mold Material:
- Sand Casting: Uses sand as the mold material.
- Metal Casting: Metal moulds are used for casting.
- By Pouring Process:
- Gravity Casting: Molten metal is poured into the mold under gravity.
- Pressure Casting: Involves the injection of molten metal into the mold under external pressure, excluding gravity.
Gravity Casting Process
Gravity casting, or metal gravity casting, involves pouring molten metal into a mold without using any external force other than gravity. This method can be broadly categorized into:
- Sand Casting: Utilizes sand molds.
- Metal Casting: Employs permanent metal molds.
Narrow Definition: Specifically refers to metal casting using gravity.
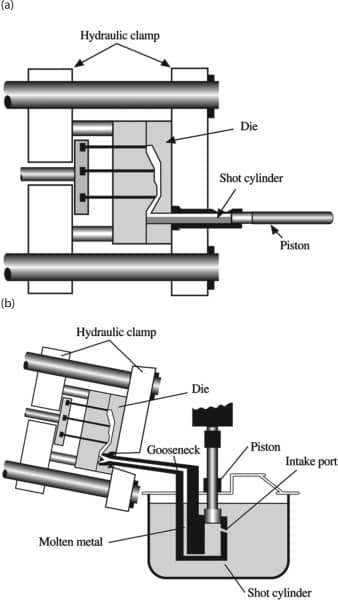
Pressure Casting: This process uses additional forces to inject molten metal into moulds, including die-casting machines, vacuum casting, low-pressure casting, and centrifugal casting.
Benefits of Gravity Casting
Gravity casting offers several advantages, making it ideal for specific applications:
- Capability to produce large parts: Gravity casting is more suitable for producing larger, thicker-walled parts that would be challenging and costly with pressure die casting.
- Formation of complex shapes: Allows intricate designs and structures.
- High-strength parts: Results in durable and robust components.
- Excellent surface finish and accuracy: Produces precise and smooth surfaces.
- High production rate: Efficient for large-scale production.
- Optimal for aluminium and light alloys: Particularly effective with lightweight materials.
- Permanent mold use: Ideal for long-lasting moulds with repeatability.
Additional benefits include:
- Corrosion resistance: Ensures durability in various environments.
- High-pressure resistance: Suitable for high-stress applications.
- Improved heat transfer performance: Enhances efficiency in heating systems.
- Flexibility in assembly: Allows for easy and adaptable installation.
Equipment for Gravity Casting
Effective gravity casting requires specialized equipment to ensure high-quality results. Key machinery includes:
- Gravity casting machines: For precise and controlled pouring.
- Lager grinders and riser cutting machines: For refining castings.
- Sand core machines and spectrometers: These are used to create and analyze mold cores.
- Aluminium liquid refining machines: To purify molten aluminum.
- CNC machines and electric stoves: For machining and melting processes.
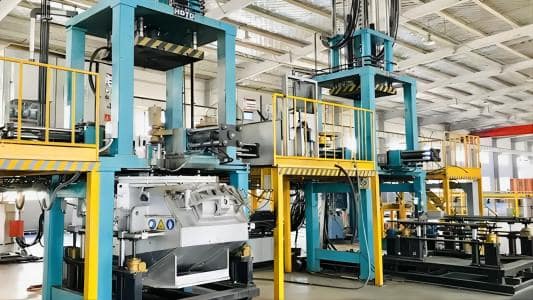
Gravity Casting Services
With decades of experience, DSW Gravity Casting offers comprehensive services to meet diverse customer needs. We handle high-volume and low-cost casting parts production, ensuring that each piece meets or exceeds international standards and customer expectations.
Capabilities of Aluminum Gravity Casting
Our manufacturing capabilities for aluminium gravity casting range from 0.5 to 30 kg, serving various industries. We utilize state-of-the-art casting processes and advanced secondary machining capabilities. Additionally, we offer value-added services such as powder coating, anodizing, painting, and assembly.
Capabilities of Die Casting Products
- Weight Range of Die Castings: 0.5 kg – 20 kg
- Annual Capacity of Sand Castings: 1,000 tons – 3,000 tons
- Casting Tolerances: Available on request or per ISO 8062
Our process includes:
- Custom gravity castings: Catering to simple and complex shapes.
- Detailed planning: Understanding client requirements and selecting suitable designs.
- Precision execution: Ensuring correct operations and superior product quality.
Applications: Our gravity casting services are ideal for various industries, including valve and pump manufacturing, automotive parts, agricultural machinery, railroad freight cars, logistics equipment, and construction machinery.
Aluminum Gravity Casting Vs. High-pressure Die Casting
Aspect | Gravity Casting | Die Casting |
Process | – Molten aluminium is poured into a mold using gravity. | – Molten aluminium is injected into a mold using high pressure. |
– No external pressure is applied. | – Typically automated. | |
Molds/Tooling | – Uses steel or cast-iron molds (permanent molds). | – Uses complex, high-precision steel molds. |
– Lower cost compared to die casting molds. Cast Iron, Steel (Low-Carbon Steel), Aluminum Alloys | – Higher cost but suitable for mass production.High-Strength Steel (H13, SKD61, H11, A2, D2), Hardened Steel | |
Production Volume | – Low to medium production volumes. | – High production volumes. |
Surface Finish | – Rougher surface finish; additional machining may be required. | – Smoother surface finish with finer details. |
Complexity | – Suitable for simpler shapes. | – Allows for intricate designs and thinner walls. |
Cost | – Lower upfront tooling costs. | – Higher initial tooling costs. |
– Higher per-piece cost due to slower production. | – Lower per-piece cost in high volumes. |
Thickness of wall in casting
Gravity Casting | High pressure Die Casting |
Wall thickness is generally thicker due to insufficient external pressure to fill thin sections. The typical minimum wall thickness is around 5-10 mm, depending on the casting design. | – Die casting allows for thinner walls because of the high-pressure injection. Typical minimum wall thickness can go as low as 1-2 mm, depending on the alloy and process control. |
Summary of Thickness Considerations:
- Gravity Casting is better suited for thicker and simpler parts, such as engine blocks or large structural components.
- Die Casting excels in producing lightweight, thin-walled, and detailed components, such as housings or electronic enclosures.
Die casting is the better choice if your project requires lightweight parts or high precision. However, for thicker, structural components with less emphasis on surface finish or thin walls, gravity casting is more economical.
Aluminum Alloy Difference
Aspect | Gravity Casting | Die Casting |
Alloy Composition | Common alloys: A356, A380, Al-Si alloys. | Common alloys: A380, A383, ADC12, Al-Si, Al-Zn alloys. |
Aluminum Alloy AU5GT (commonly equivalent to A356 or EN AC-42100) is typically used in gravity casting, although it can also be used in die casting in certain applications. The choice of process depends on the specific requirements of the part, such as size, complexity, mechanical properties, and production volume.
Conclusion
Gravity casting is a versatile and efficient process for producing high-quality metal parts. Manufacturers can achieve excellent results by understanding its benefits and using the right equipment. Partnering with experienced foundries like DSW ensures that every casting project meets the highest standards of quality and precision.
No comment