Die Casting Dies: Design, Development, and Advantages
Die casting is a highly efficient manufacturing process used to produce precisely dimensioned, smooth, or textured metal parts. Utilizing molten metal injected under high pressure into reusable die casting dies, die casting provides a cost-effective solution for mass production of non-ferrous metal parts. Originating in the early 19th century, die casting has evolved significantly, playing a pivotal role in various industries, including automotive, aerospace, and consumer electronics. This article will explore the intricacies of die cast dies, from their design and development to the advantages and disadvantages of the process.
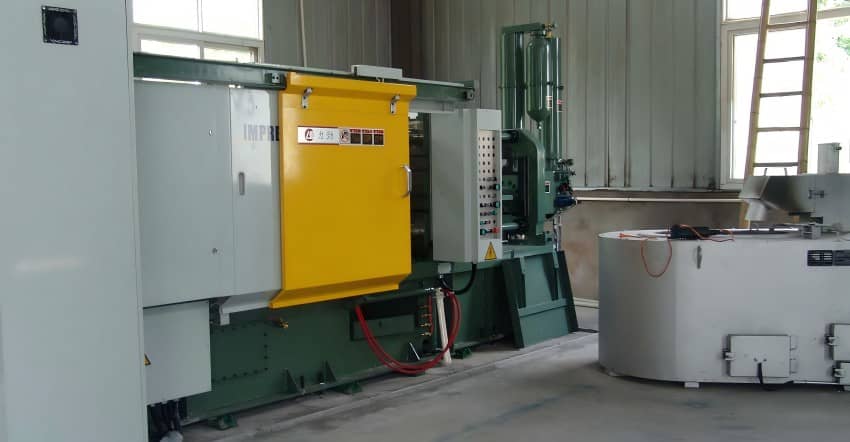
Understanding Die Casting Molds
Metallic Permanent Molds
A die casting mold is a metallic permanent mold used with a die casting machine. It contains the mold cavity, which forms the contours and dimensions of the casting. The liquid die casting alloy is fed through channels known as the gating system.
Components of a Die Casting Mold
A die casting mold typically comprises the fixed (stationary) mold half and the movable (ejector) mold half. The stationary half is mounted on the machine’s fixed plate, while the ejector half is attached to the movable plate and contains the casting ejector. The two halves are closed and held together by the die locking force during casting. The surface between the halves is known as the mold parting plane. Core slides, operated mechanically or hydraulically, demold cavities or undercuts.
Schematic Construction and Standardization
Figures often illustrate the schematic construction of die casting dies. The stationary die half includes the pattern and mounting plates, while the movable half contains the ejector and associated components. The tool parts of die casting molds are standardized in DIN 16750:1991, and the requirements for metal molds for non-ferrous alloys are outlined in EN 12891.
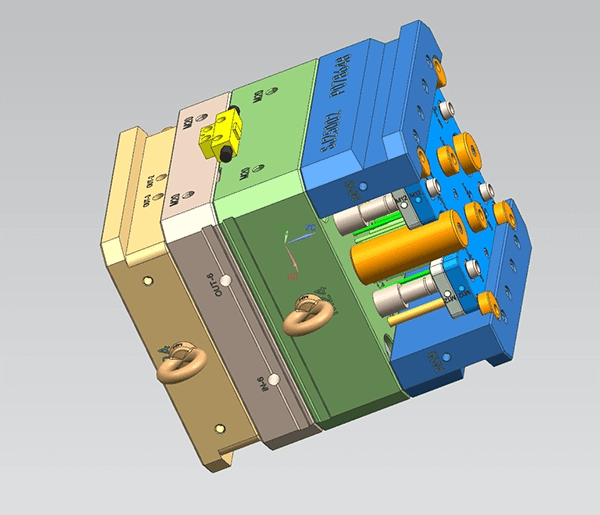
High-Pressure Die Cast Dies
High-pressure die cast dies are renowned for producing thousands of high-quality molded casts quickly using a single mold. This method ensures uniform quality and accuracy, making it a cost-effective choice for manufacturing premium-quality, near-net-shape parts.
High-pressure die casting (HPDC) involves using specialized dies to produce high-quality metal parts efficiently. Here are the primary types of HPDC dies:
Types of High-Pressure Die Casting (HPDC) Dies
- Hot Chamber Dies
Known also as “gooseneck,” hot chamber dies are distinguished from others by a mechanism that submerses the injection system of the die-casting machine in molten metal.
Parts include a piston, gooseneck, and nozzle.
It is suitable for low-melting-point alloys such as zinc, magnesium, and tin, allowing for quick and efficient injection.
Manufacturing finds common uses for highly precise tiny parts, including components for electronics and automobiles.
- Cold Chamber Dies
In a cold chamber, the molten metal is manually poured into a separate chamber and then injected into the mold.
It features a cold chamber and a separate injecting cylinder.
It is designed explicitly for high-melting-point alloys such as copper, magnesium, and aluminum, providing a longer die life and improved temperature control.
Larger and more complex items, such as structural components in the automotive and aerospace sectors and engine blocks, typically utilize this type of die.
- Multi-Cavity Dies
Multi-cavity dies allow for the simultaneous creation of multiple pieces from a single mold.
Components: Utilize multiple cavities within a single die to enhance output effectiveness.
Benefits include shortened manufacturing times and costs and the best die utilization.
Applications: Made for industrial parts and consumer goods, among high-volume components.
- Single-Cavity Dies
These single-cavity dies are designed to produce a single cavity for the intended part form.
Benefits include excellent accuracy and quality, perfect for pieces needing exact specifications.
Applications: Appropriate for low-volume or specialty manufacturing runs when outstanding detail and quality are absolutely vital.
- Insert Dies
In the case of insert dies, the main die receives detachable inserts to produce varying geometries or features for the casting.
Components: Included are replaceable, modifiable, interchangeable inserts.
Advantages: The same die can generate multiple part characteristics, thereby saving costs and providing flexibility.
Applications: Applied for parts needing different interior geometries or features, including integrated features in an automobile component.
- Core Dies
Core dies create internal cavities or intricate geometries within the casting.
Components include slides or core pins creating interior voids or forms.
Benefits include creating hollow or multi-chamber sections with intricate internal details.
Typical application uses include engine components and housings in parts needing internal channels or structural voids.
- Straw Dies
Designed to generate parts with extremely thin walls, straw dies—also called thin-wall dies.
It features elaborate thin wall designs and cooling passages.
Benefits include the ability to create highly precise and detailed, lightweight parts.
These include the consumer goods and electronics sectors, which require thin-walled, lightweight components.
Each type of HPDC die is tailored to specific materials, production requirements, and part designs, ensuring optimal efficiency and quality in the die casting process.
Advantages of HPDC Dies
DSW provides custom zinc and aluminum die casting mold production services. Their first-class engineering team oversees all aspects of tooling and the injection process, ensuring the development of high-quality dies. Key advantages of HPDC dies include:
-
- First-class engineering guarantees the design’s accuracy and efficiency.
- In-house tool design lets one provide specialized solutions that fit particular requirements.
- We manage every tool element in-house, from design to manufacturing.
- Optimizing the casting process will help to improve the injection process parameters.
- Using quality materials can enhance the performance and durability of superior mold materials by increasing their hardness.
- Predicting molten metal flow will help you better design molds.
- Excellent efficiency and reproducibility help guarantee constant quality across large manufacturing runs.
Die Casting Mold Manufacturing Process
Steps in Manufacturing Die Casting Molds
- Mold Creation: Die casting molds are created in at least two sections for proper casting removal.
- Mounting: The machine firmly fixes one stationary and one moveable section.
- Clamping: Tightly fastened together are the halves.
- Injection: The die cavity receives molten metal, which quickly solidifies there.
- Ejection: The halves separate, and the casting is ejected.
Construction of HPDC Dies
High-pressure die casting dies are made from premium, heat-resistant steel grades. They are designed to withstand repeated thermal shock and high pressure, enabling the production of a large quantity of small to medium-sized castings with high accuracy.
Additional Considerations in Die Casting Mold Design
Factors to Consider
Several factors should be considered before starting a die casting mold development project, including:
-
-
- Gate calculation, feeding speed, and fill time: Ensuring optimal flow of molten metal.
- Press size and clamping forces calculation: Matching the mold design with machine capabilities.
- Shot sleeve choice and calculation: Ensuring proper injection of molten metal.
- Venting and overflows: Preventing defects and ensuring smooth casting.
- Establishing machining stock: Allowing for post-casting machining processes.
-
Advantages of Die Casting Mold Development
Die casting offers numerous benefits, including:
-
-
-
- High thermal and electrical conductivity: Ideal for electronic and thermal applications.
- Good processing properties: Ease of machining and finishing.
- EMI/RFI isolation: Shielding electronic components from electromagnetic interference.
- Enhanced corrosion resistance: Prolonging the lifespan of cast parts.
- Greater strength and hardness: Providing durable and robust components.
- Near limitless shape possibilities: Allowing for complex and intricate designs.
- Improved dimensional accuracy: Ensuring consistency and precision in mass production.
- Fast production times: Reducing lead times and increasing efficiency.
- The ability to cast external threads and over-mold steel inserts: Offering versatility in design and functionality.
-
-
High-Pressure Die Casting in DSW
DSW has been enhancing its aluminum die casting mold capabilities since 2002, with a range of die casting machines and a daily yield of one ton. They emphasize the importance of mold quality, working closely with qualified vendors to ensure high standards in design, material selection, and production. By incorporating advanced technologies and best practices, DSW consistently delivers high-quality die casting solutions to meet diverse industry needs.
Challenges and Solutions in Die Casting Mold Development
Common Challenges
- Thermal Fatigue: Repeated heating and cooling cycles can cause mold materials to degrade.
- Porosity: Gas entrapment can lead to defects in the final cast product.
- Dimensional Variations: Inconsistent cooling rates can cause shrinkage and warping.
Solutions
- Advanced Materials: Using heat-resistant and durable materials can mitigate thermal fatigue.
- Vacuum Die Casting: Reducing gas entrapment and porosity.
- Precision Engineering: Ensuring uniform cooling and accurate mold design to minimize dimensional variations.
Future Trends in Die Casting
Innovations to Watch
- Automated Systems: Increasing efficiency and reducing human error through automation.
- Sustainable Practices: Utilizing eco-friendly materials and processes to minimize environmental impact.
- Advanced Simulations: Enhancing mold design and process optimization through sophisticated simulation tools.
No comment