Designing zinc alloy die castings requires a strategic approach to balance form, functionality, and cost-efficiency. By considering critical factors like mold structure, wall thickness, draft angles, and shrinkage, you can ensure that your zinc die casting designs are optimized for performance and manufacturability.
What is a Zinc Alloy?
Zinc alloys are metals composed of zinc as the primary component and at least one additional element. These alloys offer several advantages over pure metals, including enhanced uniformity, corrosion resistance, and improved physical, chemical, and electrical properties. Because of these properties, zinc alloys are widely used in die casting applications.
Why Choose Zinc Die Castings?
Zinc die casting is a versatile and precise solution for numerous industries. Its capacity to manufacture net-shaped components eliminates the need for costly post-casting machining. Zinc has more excellent physical and mechanical qualities than aluminium or magnesium, resulting in a higher-quality finish. Furthermore, zinc is one of the most economical metals for die casting, providing a perfect balance of performance and cost.
Reducing Costs with Zinc Die Castings
The low melting temperature of zinc results in lower energy consumption during production. Additionally, zinc casting alloys are gentler on tooling, leading to longer tool life—up to 10 times longer than aluminum and 5 times longer than magnesium dies. This extended tool life reduces downtime, maintenance, and capital investment, ultimately improving overall production efficiency.
Industries Benefiting from Zinc Die Castings
Zinc die castings are widely used in construction, electronics, automotive, and recreation industries. Zinc alloys offer superior durability and cost-efficiency, making them ideal for high-volume production. Furthermore, zinc alloy processing is environmentally friendly, allowing manufacturers to produce millions of parts with a single set of tools.
Designing Zinc Alloy Die Castings
Designers should understand hot chamber die casting machinery, die casting processes, basic mold structures, and manufacturing procedures. They should achieve design rationality, processability, manufacturability, and cost-effectiveness.
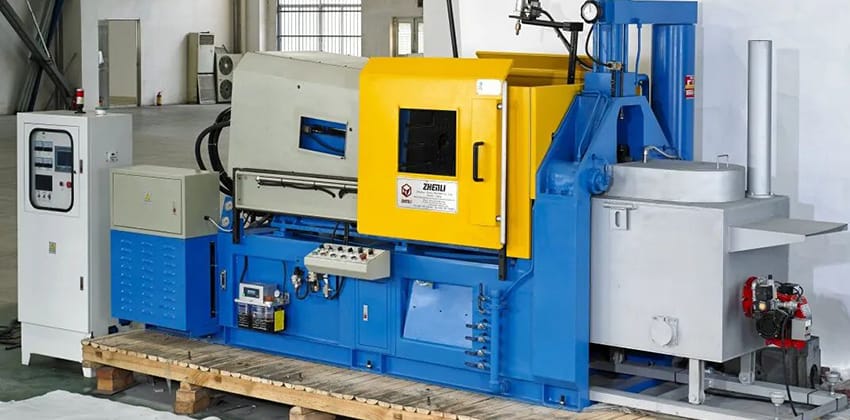
The structural design of die castings is a crucial initial phase in die casting production. A logical and process-oriented design dramatically influences the smooth progression of subsequent tasks. This includes considerations such as selecting the parting line, placing the inner gate, arranging the ejection mechanism, designing the mold structure, understanding alloy solidification shrinkage patterns, ensuring casting precision, and identifying casting defects. All of these aspects depend on the processability of the die-casting itself.
The processability of die casting structures involves the following fundamental principles:
- Eliminating internal side concavities within the casting to simplify mold complexity.
- Ensure uniform wall thickness throughout the casting. Adding reinforcements can help mitigate wall thickness variations and reduce the likelihood of defects such as porosity, shrinkage, deformation, foaming, and cracking.
- Avoiding deep holes and cavities on the casting. Thin cores are prone to bending or breakage, while inadequate air exhaust in deep cavity locations can result in filling defects.
- Designing castings that facilitate easy demolding and core extraction from the mold.
- Place parting lines and gates thoughtfully to optimize metal flow and minimize defects. Ensure the inner gate is positioned to effectively fill the mold without trapping air.
Considerations for wall thickness
Greater wall thickness in zinc alloy castings leads to reduced tensile strength.
Increased wall thickness affects how the metal liquid fills the cavity, ultimately impacting casting surface quality.
Excessive thickness in die castings increases metal material consumption and associated costs.
There is often a misconception in die casting design that thicker walls result in improved strength and rigidity. However, increased wall thickness leads to decreased mechanical properties for die castings. During the die casting process, rapid cooling of the metal liquid upon contact with the cavity surface forms a fine-grained structure layer, approximately 0.3mm thick. Therefore, die castings with thinner walls exhibit superior mechanical properties.
Requirements for designing zinc alloy die castings:
Proficiency is essential. Conversely, die castings with thicker walls have larger grain sizes in the centre layer, making them more susceptible to defects such as sand holes, shrinkage holes, air pockets, and surface depressions. This diminishes their mechanical properties as wall thickness increases.
As thickness escalates, alloy consumption and costs also increase. However, basing the minimum wall thickness solely on structural considerations may result in suboptimal liquid metal filling and subsequent defects.
Therefore, while meeting product functionality requirements, achieving optimal formability and processability with minimal metal consumption is ideal, with a preference for uniform wall thickness.
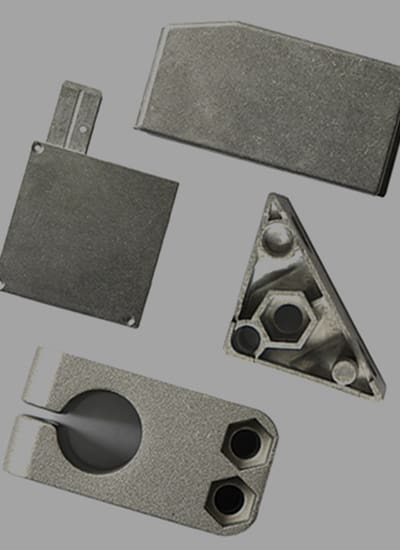
Reinforcement
Zinc die cast parts typically have uniform wall thickness. However, increasing the wall thickness is not recommended to enhance their strength and rigidity or prevent deformation. Instead, appropriate thin-wall reinforcements should be used to achieve these objectives.
Reinforcements should be symmetrically arranged with uniform thickness to avoid metal accumulation. The thickness of reinforcements is generally taken as 2/3 to 3/4 of the wall thickness of the die casting. The reinforcements should have a demolding slope ranging from 0.5 degrees to 1.5 degrees to facilitate demolding.
Fillets
Fillets play a crucial role in ensuring a smooth flow of molten metal, improving filling characteristics, facilitating the expulsion of gases, and preventing stress concentration and cracking caused by sharp corners. Fillets are essential to ensure a good external appearance after plating, particularly for die castings requiring electroplating.
Draft Angles
Zinc die cast parts should have draft angles as large as possible to facilitate demolding and reduce ejection force, core withdrawal force, and mold wear. This helps minimize friction between the die casting and the mold, makes it easier to remove the casting, and prevents surface abrasion, resulting in a smooth surface.
Text, Marks, Patterns
Raised patterns greater than 0.3mm in height should be used during die-casting to accommodate mold manufacturing characteristics.
Film technology can transfer coloured text, marks, and patterns onto the die casting’s surface.
After die casting, laser marking can be utilized to mark text, marks, and patterns on the surface of the casting, enabling the inclusion of very fine text.
Shrinkage Allowances
Shrinkage is a common occurrence in metal casting, and it’s vital to account for it during the design phase:
- Understanding Shrinkage Rates: Zinc alloys typically experience free shrinkage rates between 0.6% and 0.8%. Constrained shrinkage is lower, at about 0.3% to 0.6%. These rates must be factored into the design to ensure the final part meets dimensional specifications.
- Design Adjustments: To minimize defects related to shrinkage, consider creating features that allow for controlled shrinkage, such as strategically placed fillets and gradual transitions in geometry.
Surface Finishes and Textures
The surface finish of die castings can significantly affect their performance and aesthetic appeal:
- Design for Quality: When designing parts, consider the desired surface finish. Features like raised text, logos, and patterns can be integrated into the design to enhance branding and functionality.
- Post-Casting Treatments: If a specific finish is required, such as electroplating, ensure that the design supports these processes. For example, fillets can help achieve a better surface finish, especially in areas subject to additional treatment.
What Is A Common Applications Of Zinc Die Castings?
Common applications of zinc alloy castings include:
Automotive Components: Used for parts like transmission cases, engine covers, and decorative trim due to their strength and lightweight properties.
Electronics Housings: Ideal for enclosures of electrical devices, connectors, and components because of their excellent shielding and heat dissipation.
Industrial Equipment: Found in machinery parts, tools, and fixtures that require durability and precision.
Consumer Products: Used in household items like locks, hardware, and appliances due to their aesthetic appeal and corrosion resistance.
Medical Devices: Utilized in various medical equipment and instruments where precision and reliability are critical.
Aerospace Components: Employed in non-structural components that benefit from the material’s lightweight nature and strength.
Zinc die castings are favored in these applications for their excellent mechanical properties, intricate design capabilities, and cost-effectiveness.
Conclusion
Designing zinc alloy die castings requires a careful balance between functionality, manufacturability, and cost-efficiency. By adhering to the principles outlined in this article—such as maintaining uniform wall thickness, simplifying mold design, and incorporating reinforcements—manufacturers can create high-quality components that meet rigorous performance standards.
As industries increasingly prioritize sustainability and efficiency, zinc die casting stands out as a versatile solution for a wide range of applications. If you’re considering zinc die casting for your next project, leveraging these design principles will ensure you maximize the benefits of this exceptional manufacturing process.
No comment