Porosity in ADC12(A383)Die Casting: Causes and Reduction Methods
ADC12 is a widely used aluminium alloy in die casting, known for its excellent mechanical properties, corrosion resistance, and machinability. However, porosity remains a common challenge in ADC12 die casting, which can potentially compromise the quality and performance of the final products. This article examines the causes of porosity in die casting and outlines effective methods to reduce it, ensuring superior casting outcomes. The A383 alloy is comparable to ADC12 in terms of composition and properties, offering excellent fluidity and corrosion resistance. This makes it ideal for producing thin-walled, intricate castings commonly used in the automotive and electronics industries. It ensures dimensional accuracy and durability in applications requiring high strength and reliability.
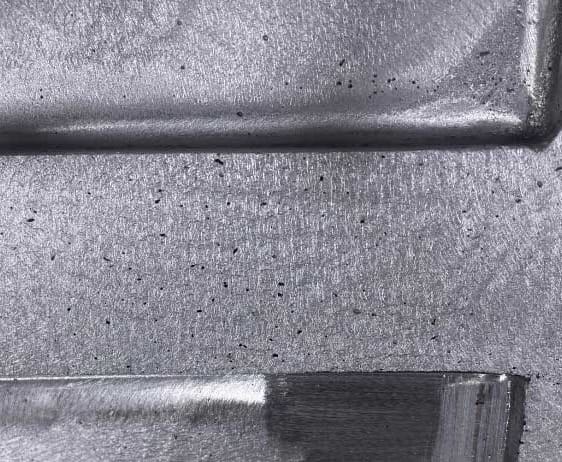
What is Porosity in Die Casting?
Porosity refers to voids, cavities, or holes within a casting’s metal structure. These imperfections can occur due to trapped air, shrinkage during solidification, or gases generated during the die casting. Porosity adversely affects the casting’s mechanical strength, surface finish, and pressure tightness, making its mitigation critical for high-performance applications.
Causes of Porosity in ADC12 Die Casting
- Gas Entrapment
-
- Source: Air can become trapped in the molten metal during injection or turbulence in the gating system.
- Impact: Leads to gas porosity with spherical-shaped voids dispersed throughout the casting.
- Primary Factors: High injection speeds, poor venting, or inadequate gating design.
- Appearance: Gas-induced porosity typically results in smooth, round, or spherical voids. This is because gas bubbles form in the molten metal and, as the metal solidifies, they leave behind soft and uniform holes.
-
- Shrinkage Porosity
- Source: This occurs during the cooling and solidification process when the material volume decreases and insufficient molten metal is available to fill voids.
- Impact: Results in irregularly shaped cavities, typically near thicker casting sections.
- Primary Factors: Improper mold design or uneven cooling rates.
Comparison of Gas and Contamination Porosity
Factor | Gas Porosity | Contamination Porosity |
Cause | Trapped gases, such as air or steam during the injection process | Presence of foreign particles or impurities in the molten metal |
Location | Typically near the centre or surface of the casting | Mostly near the surface, where contaminants accumulate |
Appearance | Small, spherical voids or smooth, round holes | Irregular, sharp-edged voids, rough, and uneven boundaries |
Impact on Material | Weakens the material, reduces strength, and impacts durability | Reduces material integrity, may lead to poor surface finish or internal defects |
Prevention | Improve venting, minimise moisture, and control injection speed | Use proper degassing and filtration, ensure clean equipment and metal handling |
Mold Design Issues
- Poorly Designed Gating and Runners: These can cause turbulence or insufficient mold filling, increasing the risk of porosity.
- Inadequate Vents: Poorly vented moulds trap air and gases, creating porosity during solidification.
- Alloy Characteristics
- Source: The composition of ADC12 may release hydrogen or other gases during melting, contributing to gas porosity.
- Impact: Increases susceptibility to internal defects unless degassing is performed.
- Die Design and Process Conditions
- Source: Suboptimal runner and gate dimensions or insufficient mold venting.
- Impact: Causes air and gas to remain trapped during the casting cycle.
Methods to Reduce Porosity in ADC12 Die Casting
- Optimise Mould and Die Design
- Adequate Venting: Incorporate vents and overflow channels to allow trapped air and gases to escape.
- Gating System Improvements: Use well-designed runners and gates to minimize turbulence and air entrapment.
- Control Injection Parameters
- Moderate Injection Speeds: Avoid excessive speeds to reduce air turbulence.
- Balanced Pressure Control: Ensure consistent injection pressure to fill moulds evenly without introducing voids.
- Degassing
- Gas Removal: Use fluxes or inert gas during the melting process to eliminate dissolved hydrogen from the molten metal.
- Vacuum-Assisted Casting: Employ vacuum technology to reduce the risk of gas porosity.
- Thermal Management
- Uniform Cooling: Use chills or cooling channels in the mold to ensure even solidification.
- Adjust Pouring Temperature: Maintain appropriate molten metal temperatures to minimise shrinkage effects.
- Material Handling and Preparation
- Proper Storage: Store raw materials in a dry location to prevent moisture contamination.
- Filtration: Use ceramic foam filters to remove impurities that might generate gas during casting.
Porosity Detection Methods
Advanced non-destructive testing methods are employed to identify and quantify porosity in castings:
- X-Ray Inspection: Reveals internal voids and defects without damaging the casting.
- Ultrasonic Testing: Detects variations in density that indicate porosity.
- Pressure Testing: Evaluate the leak-tightness of the casting, particularly for pressure-sensitive components.
How Does Porosity Affect Automotive Components?
Porosity, a common issue in die casting, can significantly impact automotive components’ performance, reliability, and longevity. It occurs when air pockets or voids form within the metal during the casting process, leading to reduced mechanical strength, potential leaks, and compromised structural integrity.
Automotive Components Commonly Made by Die Casting
Die casting is widely used in the automotive industry to produce high-precision and strong components. However, porosity in these parts can pose challenges, especially for critical applications. Below is a categorised list of automotive and truck components that rely on die casting:
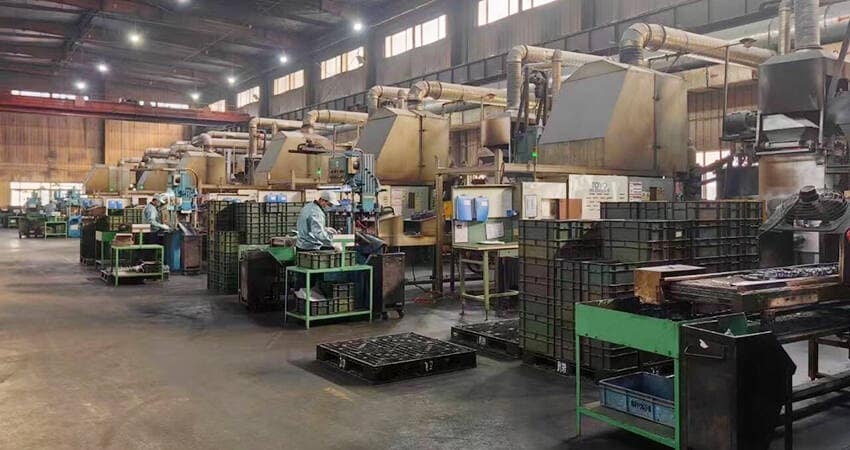
1. Automotive Components
- Engine Components: Engine blocks, cylinder heads, throttle bodies, thermostat housings, bed plates, and oil sumps.
- Powertrain Parts: Clutch cases, torque converter housings, transmissions, and valve body castings.
- Air and Fuel Systems: Inlet manifolds, oil and fuel rails, pump bodies, and EGR hardware.
- Cooling Systems: Water pumps and timing chain covers.
- Forced Induction Systems: Turbochargers and superchargers.
2. Truck Components
- Heavy-Duty Engine Parts: Turbocharger housings, crankcases, and pistons.
- Chassis Components: Reinforcement brackets and cross members.
- Fuel System Parts: Diesel injector housings and fuel pump covers.
- Brake and Suspension Systems: Brake callipers, suspension mounts, and hubs.
3. Automotive Components
- Electric Vehicles (EVs): Battery enclosures and motor housings.
- Trailers: Hitch couplers, tow hooks, and axle mounts.
- Cab Components: Door handles, mirrors, and structural hinges.
Benefits of Die Casting for Automotive Applications
Die casting is preferred for its precision, strength, and cost-effectiveness, making it ideal for producing complex shapes with tight tolerances. Components benefit from high-dimensional accuracy, consistent quality, and reduced machining requirements.
However, managing porosity during the die-casting process is crucial to fully realise these advantages, especially in applications that demand high mechanical strength, leak resistance, and durability. Effective porosity control enhances the reliability of automotive components, thereby contributing to the development of safer and more durable vehicles.
Conclusion
Porosity is a significant quality challenge in ADC12 die casting, but it can be effectively managed through optimised design, precise process controls, and careful material handling. Implementing these methods ensures that ADC12 castings meet the stringent requirements for strength, durability, and reliability in the automotive, electronics, and consumer goods industries. By addressing the root causes of porosity, manufacturers can enhance product quality, reduce defects, and achieve greater customer satisfaction.
No comment