Deliver Excellence in Die Cast Metal Parts
As aluminum die casting manufacturers, we distinguish ourselves through a process that consistently yields high-quality die casting parts. Each of our seven facilities is dedicated to a specific manufacturing process to ensure precision, enabling our skilled technicians to concentrate on individual productions. Our ten die casting machines, each equipped with its own melting furnace, have capabilities ranging from 300 to 1,600 tons. This versatility allows us to accommodate various component sizes during production.
Raw Material Inspection:
1. Chemical Composition Analysis: Samples of the raw aluminum material are taken and analyzed to determine their chemical composition. This analysis ensures the material meets the required alloy composition for the die casting process. Chemical composition analysis is typically performed using spectroscopy or wet chemistry techniques.
2. Mechanical Testing: Mechanical tests, such as tensile testing or hardness testing, may be conducted to evaluate the strength and mechanical properties of the raw aluminum material. This helps ensure that the material will withstand the stresses of the die casting process and meet the performance requirements of the final product.
3. Microstructural Analysis: Microstructural analysis involves examining the internal structure of the raw aluminum material under a microscope.
Melting Processing
During the aluminum die casting process, the aluminum ingots are melted in a melting furnace at a die casting machine station. Each station is equipped with its melting furnace to ensure efficient operation. The only manual step in this process is the placement of the ingot into the furnace by a human operator. Once the ingot is loaded, the rest of the casting process, including the pouring of molten aluminum into the die cavity, is fully automated. This automation helps ensure consistency, precision, and efficiency in producing aluminum castings.
Casting Processing
After the aluminum ingots are melted in the melting furnace, the resulting molten aluminum is injected into the die. Our die casting parts range encompasses various sizes and weights, requiring different machines for production. Notably, we utilize a 1,600-ton machine capable of casting most powertrain components. This comprehensive range of machines ensures versatility and efficiency in meeting diverse casting requirements.
Precision Die Casting
Precision die casting is a specialized manufacturing process that involves injecting molten metal into a mold cavity under pressure. This method is widely used to produce intricate and high-precision metal parts with tight tolerances and excellent surface finishes
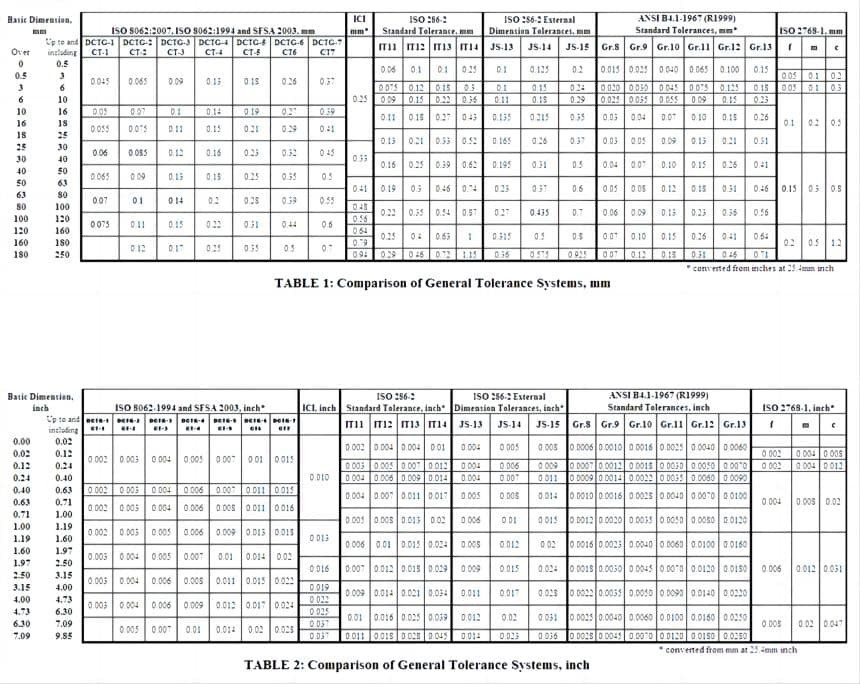
The ISO 8062 standard specifies dimensional tolerances for castings, which are categorized into different grades (e.g., CT4, CT5, CT6). Each grade represents a specific tolerance range, with lower numbers indicating tighter tolerances.
Quality Control-final Inspection on casting
With technological advancements, our quality assurance methods have evolved beyond traditional practices. Instead of relying on cutting the product to test for porosity, we utilize state-of-the-art X-ray machines. These machines enable us to conduct non-destructive testing, providing accurate assessments of component integrity without compromising their structural integrity.
In addition to X-ray inspection, we implement several other quality control measures throughout the production process to ensure the highest standards are met:
1. Visual Inspection: Skilled technicians perform visual inspections at various stages of production to detect any surface defects, such as cracks, porosity, or irregularities.
2. Dimensional Accuracy Checks: Precise measurements are taken using advanced metrology equipment to verify dimensional accuracy and adherence to design specifications.
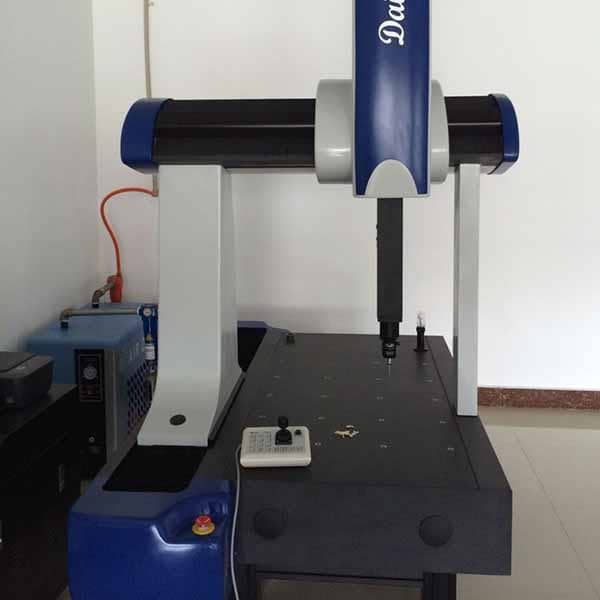
3. Material Testing: To ensure they meet specified requirements, samples of the castings are subjected to material testing, including chemical composition analysis and mechanical property testing.
4. Process Monitoring: Our production process is continuously monitored and adjusted to maintain optimal conditions and minimize variability in casting quality.
5. Training and Certification: Our team undergoes regular training and certification to ensure proficiency in operating machinery, interpreting test results, and adhering to quality standards.
To ensure the quality of the surface finish, we employ several control measures:
• Visual Inspection: Trained inspectors examine the components visually at various stages of the surface finishing process to detect defects or inconsistencies.
• Thickness Measurement: For painted or coated components, the thickness of the surface finish is measured using precision instruments to ensure uniform coverage and adherence to specifications.
• Adhesion Testing: Adhesion tests assess the bond strength between the surface finish and the component substrate, ensuring durability and longevity.
• Salt Spray Testing: Components may undergo salt spray testing to evaluate the corrosion resistance of the surface finish under harsh environmental conditions.
Once the components are completed to specifications and the surface finish quality is verified, they are carefully packaged to prevent damage during transit and shipped to the customer. This meticulous attention to detail at every stage of the process ensures that our customers receive components of the highest quality that meet their exact requirements.
Benefits of Die Casting
1. Advantages of Aluminum: Aluminum offers several advantages over traditional materials like steel. It possesses dimensional solid stability while being significantly lighter, making it an ideal choice for industries seeking lightweight components and machines.
2. Cost-Effective Solution: By utilizing aluminium die casting, we provide a cost-effective solution to companies in industries such as automotive and agriculture. Aluminium die casting allows for highly precise production of complex shapes, reducing the need for additional machining and finishing processes, thereby lowering overall production costs.
3. Weight Reduction: Aluminum’s lightweight nature helps reduce the weight of components and machines, leading to several benefits. For example, lighter vehicles in the automotive industry result in improved fuel efficiency, lower emissions, and enhanced handling characteristics. This weight reduction is crucial for meeting stringent regulatory standards and consumer demands for more environmentally friendly and efficient vehicles.
4. Increased Opportunities in the Automotive Industry: With the rise in electric vehicle production and the ongoing focus on sustainability, there is a significant opportunity for growth in the automotive sector for aluminium-based components. Aluminum’s lightweight properties contribute to electric vehicles’ overall efficiency and performance, further driving its adoption in the industry.
5. Superior Handling and Performance: Vehicles and machines manufactured with aluminium components benefit from superior handling and performance due to the reduced weight. This results in improved acceleration, braking, and overall agility, enhancing the user experience and providing a competitive edge in the market.
By offering aluminum die casting solutions, we help our customers save on weight and cost while providing superior performance, efficiency, and sustainability components.
No comment