What Is Cold Chamber Die Casting?
The Cold-Chamber Die Casting is perfect for metals like aluminium alloys, zinc alloys, brass, and copper, which require super-high temperatures to melt. Unlike hot chamber die casting, cold chamber keeps the molten metal separate from the machine. Think of it like having a pot of melted metal next to an injection machine. In a cold chamber, we scoop the metal from the pot and pour it into a special chamber in the machine. Then, a powerful plunger shoves the molten metal into the mold under high pressure, ensuring it fills every tiny crevice. This separation is why it’s called “cold chamber.”
Partner DSW
At DSW, we’ve been pushing the boundaries of cold chamber die casting for over 20 years. We leverage cutting-edge technology and a team of experienced professionals to deliver exceptional results. Whether you need a single prototype or high-volume production runs, DSW is your trusted partner.
Ready to discuss your project?
Contact our team today for a free consultation and quote.
Request a quote online to get started quickly.
We look forward to exceeding your expectations for cold chamber die casting excellence.
The Cold-Chamber Die Casting Process: A Step-by-Step Look
Cold-chamber die casting is a well-suited method for producing parts from metals with high melting points, such as aluminum alloys, zinc alloys, brass, and copper. Unlike hot chamber die casting, this process keeps the molten metal separate from the machine, eliminating potential corrosion issues with its injector components.
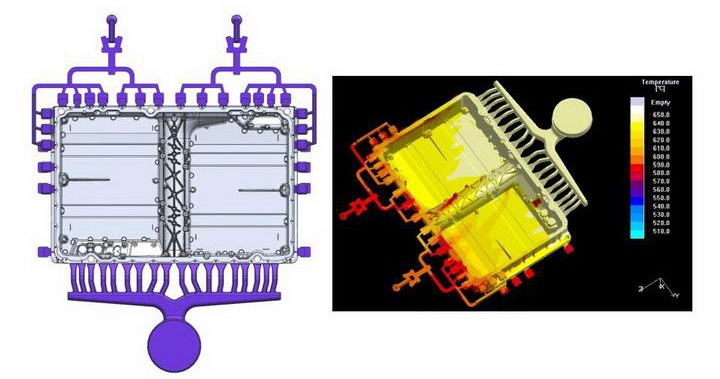
Here’s a breakdown of the key steps involved:
Melting: The metal is first melted in a high-temperature furnace capable of reaching extremely high temperatures (depending on the chosen metal).
Transfer & Injection: Once molten, the metal is carefully ladled from the furnace using a specialized tool called a ladle. This molten metal is then poured into a temporary holding chamber within the machine known as the shot chamber. A powerful plunger then forces the molten metal from the shot chamber into the mold cavity at high pressure, typically ranging from 2,000 to 20,000 psi. This high pressure ensures the molten metal fills every intricate detail of the mold.
Cooling & Solidification: The metal rapidly cools and solidifies within the mold, taking the desired shape of the final part. The mold itself is explicitly designed to create the required component geometry.
This process has several advantages, including the production of denser, more substantial metal parts and the ability to create thin-walled designs.
Cold Chamber vs. Hot Chamber Die Casting: The Key Distinction
The separation between the molten metal and the casting machine is the crucial difference between cold chamber and hot chamber die casting.
Cold Chamber Die Casting:
Metal is melted in a separate furnace reaching high temperatures.
The molten metal is then transported and poured into the machine’s chamber using a ladle.
A high-pressure plunger forces the metal into the mold cavity.
Advantages of Cold Chamber:
The Cold Chamber Die Casting Process offers several key advantages, making it ideal for manufacturing high-quality, durable parts efficiently:
1. Strength & Lightweight
Cold chamber die-cast parts are stronger and lighter than plastic injection-molded parts. The strength comes from the alloy itself, not from welding or fastenings.
2. Dimensional Accuracy & Stability
This process produces parts with tight tolerances and excellent heat resistance, ensuring dimensional stability for precision applications.
3. High-Speed Production
Cold chamber die casting allows for quick production of complex shapes with minimal or no machining. It can produce thousands of identical parts before requiring tooling changes.
4. Simplified Assembly
Integral features like bosses and studs can be cast directly into the part, reducing the need for post-production assembly. Threads and holes can also be cast.
5. Versatile Finishing
Parts can have smooth or textured surfaces and can be easily plated or finished with minimal preparation.
6. Material Flexibility
The process works well with high-melting alloys like aluminum, zinc, and brass, allowing for custom properties like increased strength, corrosion resistance, and conductivity.
7. Low Tooling Maintenance
The durable tools used in cold chamber die casting require less maintenance, reducing downtime and extending tool life.
8. Cost-Effective for High Volumes
Cold chamber die casting is economical for large production runs due to its ability to spread tooling costs across many parts.
9. Superior Surface Quality
The process results in high-quality, smooth surfaces, reducing the need for additional finishing.
10. Sustainability
It is energy-efficient, produces minimal waste, and uses recyclable materials, contributing to environmental benefits.
Cold chamber die casting is an efficient, cost-effective method for producing strong, precise, and high-quality parts. It is particularly suitable for high-volume production and complex designs, offering benefits such as improved strength, rapid production, and reduced post-processing.
Hot Chamber Die Casting (in contrast):
Here, the molten metal is kept within a dedicated pot integrated into the machine itself.
This method is typically used for lower melting point metals like zinc and magnesium alloys.
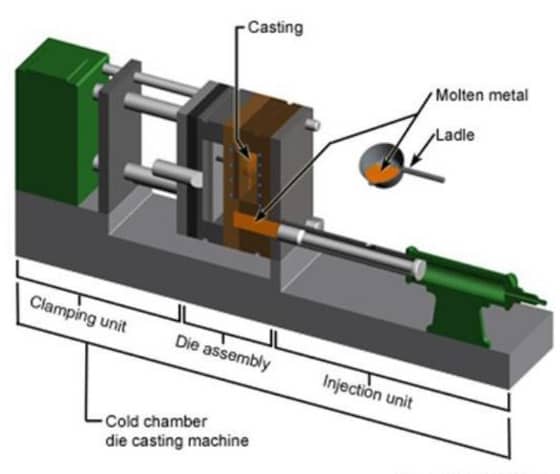
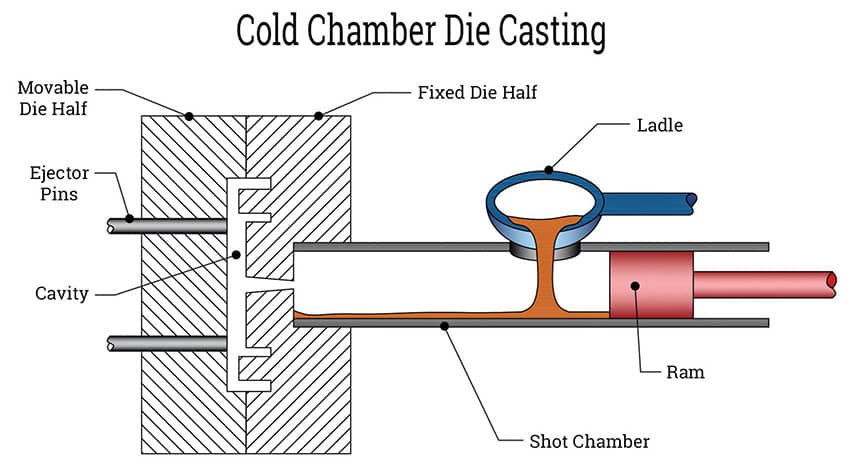
Our Cold Chamber Die Casting Machines
Our Cold Chamber Die Casting Machines
At DSW, we only use the latest and most advanced die casting machines to ensure the highest quality parts. Here are some of the models we have available:
Haitian HDC Series (180T-850T)
HII-S Series Cold Chamber Die Casting Machine(180-900T)
HII-S Series Cold Chamber Die Casting Machine(1000-2000T)
LK D series die casting machines D seriesTonnage:160-900
Assembly and Installation Services
Need help with assembly or installation? We can work with you to find solutions for tasks like:
Installing pins or threaded inserts
Machining external threads
Pre-casting holes for internal threads
DSW Cold Chamber Die Casting
Every component we manufacture is custom-designed and built to your exact specifications. We can handle production volumes ranging from a few hundred to hundreds of thousands of parts.
Start Cold Chamber Die Casting
Contact us today at +86-574-27861829 or request a quote online!
No comment