Alu Heat Sinks: Heat Conductivity and Applications
Thermal conductivity is essential in materials science, particularly for managing heat effectively. Aluminium stands out due to its exceptional thermal conductivity and is widely chosen for various applications – including aluminium heat sinks (alu heat sinks).
Aluminium’s thermal conductivity ranges between 150-237 W/m*K, providing it with the capability of efficiently dissipating heat—an essential feature of heat sinks. Aluminium is an ideal material choice because its lightweight properties and thermal efficiency work harmoniously to meet the requirements of compact designs. Furthermore, its abundance and cost-effectiveness reinforce its popularity for thermal management solutions across various industries. This article explores aluminium’s thermal conductivity properties as critical in optimising its heat sink performance across sectors.
Thermal Conductivity of Aluminum
Thermal conductivity measures a material’s ability to conduct heat and is quantified in watts per meter Kelvin (W/m·K). Aluminium exhibits high heat conductivity, typically between 150 and 237 W/m·K, depending on the alloy and temperature. This allows aluminium to effectively transfer heat away from sensitive components, making it ideal for thermal management applications.
Table 1: Thermal conductivity of Aluminum Alloys
Alloy Composition (wt.%) | Temper | Tensile Strength (MPa) | Thermal Conductivity (W/m·K) |
Al-5.5Si-4.5Cu (308) | F | 195 | 142 |
Al-6Si-3.5Cu (319) | T6 | 280 | 109 |
Al-9Si-1.8Cu-0.5Mg (354) | T6 | 380 | 128 |
Al-5Si-1.3Cu-0.5Mg (355) | T6 | 240 | 152 |
Al-7Si-0.3Mg (356) | T6 | 230 | 151 |
Al-7Si-0.5Mg (357) | T6 | 262 | 152 |
Al-9Si-0.6Mg (359) | T6 | 276 | 138 |
Al-9.5Si-0.5Mg (360) | As-cast | 305 | 113 |
Al-8.5Si-3.5Cu (380) | As-cast | 330 | 96 |
Al-10.5Si-2.5Cu (383) | As-cast | 310 | 96 |
Al-11.2Si-3.8Cu (384) | As-cast | 330 | 92 |
Al-17Si-4.5Cu-0.6Mg (390) | T7 | 250 | 134 |
Al-12Si (413) | As-cast | 300 | 121 |
Aluminium alloys, like 380 and 319, contain secondary phases such as eutectic Si and Al₂Cu, making them composites with 5-8% volume fractions. The Effective Medium Theory (EMT) can assess how these phases influence the thermal conductivity of the alloys.
Wide Applications of Alu Heat Sinks
Alu heat sinks are employed across various industries due to their superior thermal management capabilities. Here are some critical applications:
- Electronics Industry:
- Computers and Laptops: Essential for cooling processors and other critical components.
- LED Lighting: Manage heat produced by LEDs, extending their lifespan and maintaining performance.
- Power Electronics: Used in inverters, rectifiers, and other power management devices to dissipate excess heat.
- Automotive Industry:
- Engine Control Units (ECUs): Ensure optimal operating temperatures for electronic control units.
- Electric Vehicles (EVs): Manage the thermal conditions of battery packs and other electronic components.
- Telecommunications:
- Base Stations: Cool transceivers and other sensitive equipment.
- Networking Devices: Routers, switches, and modems use aluminium heat sinks to maintain performance.
- Renewable Energy:
- Solar Inverters: Manage heat generated during the conversion of DC to AC power.
- Wind Turbines: These are used in the electronic control systems of turbines.
Design of Aluminum Heat Sinks
Effective heat sink design maximizes thermal management efficiency. Key design elements include:
- Finned Design:
- Increased Surface Area: Fins, for example, can increase the efficiency of aluminium heatsinks by maximizing surface area. By increasing the surface area exposed to air, these fins allow more heat to be dissipated through convection. Aluminum’s malleability enables the creation of complex shapes like pin fins and straight fins.
- Types of Fins: Options like straight fins, pin fins, and flared fins each offer unique thermal management benefits.
- Extrusion:
- Custom Profiles: Allows for creating complex profiles that optimize heat sink performance.
- Die Casting:
- Custom Castings: Die-cast aluminium heat sinks are favoured when complex geometries, high dimensional accuracy, and high production volumes are needed. While extruded aluminium heat sinks are helpful for simpler designs and smaller production runs, die casting offers detail, strength, and efficiency advantages for more intricate and demanding applications.
- Bonded or Folded Fin Design:
- Enhanced Performance: Bonding or folding thin aluminium sheets creates heat sinks with larger surface areas and improved performance.
- Baseplate and Heat Pipes:
- Hybrid Designs: Incorporating heat pipes or copper baseplates enhances thermal conductivity and evenly distributes heat.
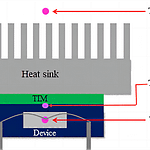
How to Use Aluminum Heat Sinks
Proper use of aluminium heat sinks involves installation, maintenance, and optimization:
- Installation:
- Mounting: Attach heat sinks using screws, clips, or thermal adhesives to ensure proper contact with the heat source.
- Thermal Interface Materials (TIMs): For optimal heat transfer, employ thermal paste or pads to fill microscopic air gaps between the heat sink and the component.
- Maintenance:
- Cleaning: Regularly clean heat sinks to remove dust and debris that could obstruct airflow and reduce efficiency.
- Inspection: Periodically check for signs of wear or damage and replace as necessary.
- Optimization:
- Active Cooling: Combine aluminium heat sinks with fans to enhance cooling performance.
- Passive Cooling: In applications where silent operation is essential, relying on natural convection alone.
Understanding aluminium’s thermal conductivity, as well as designing and implementing aluminium heat sinks, is essential for optimising thermal management solutions. Aluminium’s excellent thermal transfer properties, along with its lightweight and cost-effective nature, make it an ideal choice for heat sinks. By leveraging these benefits, industries can enhance the performance and lifespan of electronic components and systems across various applications.
No comment