Zinc alloys or Zamak are widely employed in the die-casting industry due to their low melting point, favourable fluidity, ease of welding, mechanical strength, and corrosion resistance in atmospheric conditions. This article explores the dissimilarities between two prominent zinc alloys, Zamak 5 and Zamak 3. It sheds light on their unique characteristics, composition, physical properties, mechanical properties, thermal properties, and advantages in hot chambered die-casting applications.
What is ZAMAK?
Zamak is a family of alloys primarily composed of zinc, along with aluminum, magnesium, and copper. The name Zamak is derived from the German words for the metals it contains: “Z” for Zink (zinc), “A” for Aluminium (aluminum), “MA” for Magnesium, and “K” for Kupfer (copper).
Zamak 3 and Zamak 5 Chemical Composition
Element | Zamak 3 (%) | Zamak 5 (%) |
Aluminum (Al) | 3.5-4.3 | 3.5-4.3 |
Copper (Cu) | 0.25 | 0.75-1.25 |
Magnesium (Mg) | 0.02-0.05 | 0.02-0.05 |
Iron (Fe) | 0.1 | 0.1 |
Lead (Pb) | 0.005 | 0.005 |
Cadmium (Cd) | 0.004 | 0.004 |
Tin (Sn) | 0.003 | 0.003 |
Zinc (Zn) | Balance | Balance |
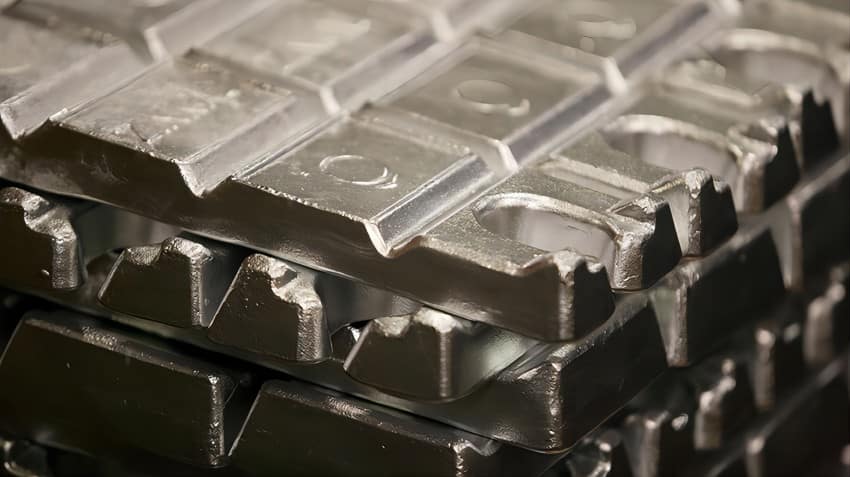
Types of Zamak Alloys
Regarding mechanical properties, Zamak 5 offers higher strength, hardness, and impact resistance than Zamak 3. It is suitable for applications that require increased durability and strength. Zamak 3, on the other hand, is known for its excellent fluidity, good dimensional stability, and ease of casting.
Mechanical Properties
Alloy | Tensile Strength (MPa) | Yield Strength (MPa) | Modulus of Elasticity (GPa) | Elongation at Break (%) | Brinell Hardness |
Zamak 3 | 268 | 208 | 96 | 10 | 82 |
Zamak 5 | 331 | 295 | 96 | 7 | 91 |
Thermal Properties
Alloy | Thermal Conductivity (W/mK) |
Zamak 3 | 113 |
Zamak 5 | 109 |
Please note that the values provided are based on standard testing and represent typical mechanical and thermal properties for Zamak 3 and Zamak 5 alloys.
Surface Finish:
Advantages of Zinc Die Casting Alloys:
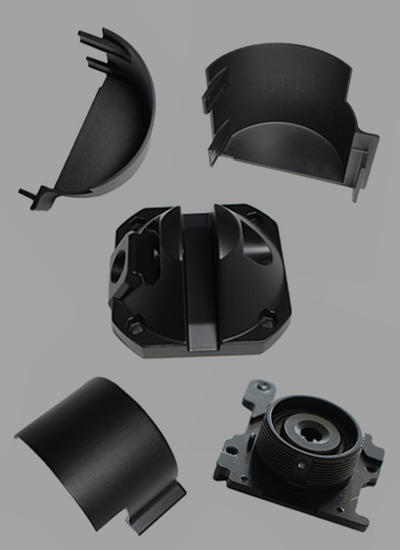
Methods to Improve Accuracy and Reduce Defects:
- Utilizing Multi-Slide and Conventional Die Casting machines based on product requirements
- Implementing Design for Manufacturability (DFM) principles during mold design to predict and address potential air bubble formations
- Enhancing process control during surface treatment to improve product yield rates
- Employing CCD visual inspection systems for comprehensive quality control and to minimize defective products
Applications of Zinc Die Casting:
Zinc alloys find widespread applications in various industries, including:
- Decoration Parts
- Industry Parts
- Communication Parts
- Automotive Parts
- Consumer Parts
- Blenders
Conclusion:
In conclusion, Zamak 5 and Zamak 3 are distinct zinc alloys with unique characteristics and advantages in die casting applications. Their differences in composition, physical and mechanical properties, as well as thermal conductivity, make them suitable for different industrial needs. Understanding these disparities can help manufacturers make informed decisions when selecting the appropriate alloy for their die casting requirements.
No comment